Most Hammer Drills Will Not Hammer Until Pressure Is
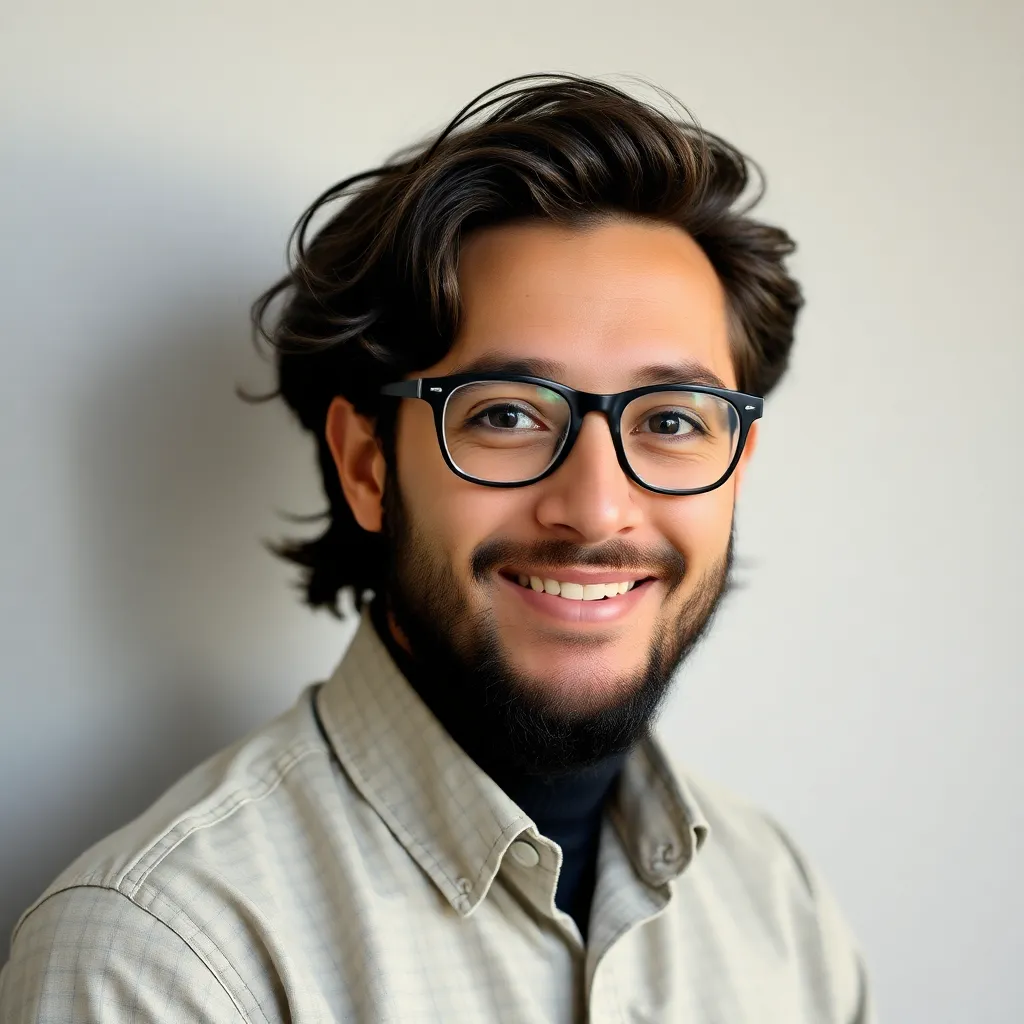
Onlines
Apr 01, 2025 · 6 min read
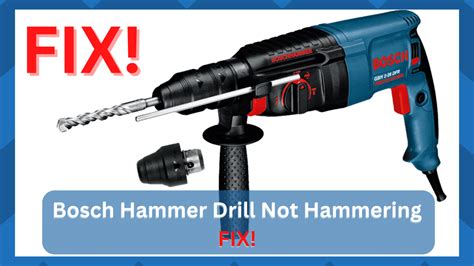
Table of Contents
Most Hammer Drills Won't Hammer Until Pressure is Applied: Understanding the Mechanism and Troubleshooting
Many users of hammer drills encounter a common issue: the hammering action doesn't activate until significant pressure is applied to the drill bit. This isn't necessarily a fault; it's often a built-in safety feature or a consequence of the drill's mechanism. This comprehensive guide dives deep into the reasons behind this behavior, troubleshooting steps, and preventative measures to ensure smooth operation of your hammer drill.
Understanding the Hammer Drill Mechanism: Why the Delay?
Hammer drills, unlike standard drills, incorporate a hammering mechanism alongside the rotational drilling function. This hammering action significantly enhances drilling speed and efficiency, particularly in masonry, concrete, and other hard materials. The delay in hammering activation, however, is often linked to several interacting factors within the drill's complex internal workings:
1. The Impact Mechanism and its Sensitivity
Most hammer drills utilize a pneumatic or electro-pneumatic system for impact. This system typically involves a piston-driven hammer mechanism. This piston doesn't activate until sufficient pressure is exerted on the bit. This is a safety feature: it prevents accidental hammering while the drill is simply rotating at low speeds or idling. The system is designed to ensure the impact force is only applied when it's needed – during drilling into tough materials. The level of pressure required for activation varies between drill models and brands, due to differences in the sensitivity of the mechanism.
2. The Role of the Clutch and Gear System
The hammer drill's clutch and gear system play a vital role in transmitting power and controlling the rotational speed. Before the hammering action kicks in, the rotational speed is often initially lower. This gear system needs to overcome a certain threshold of resistance before the hammer mechanism engages. The resistance could be due to the material itself or the pressure exerted by the user. This results in the delay where the drill rotates normally before the hammering activates. Think of it like a car's clutch – you need to press down firmly (apply pressure) before the engine's full power is delivered.
3. Rotational Speed and Impact Force Correlation
Many hammer drills correlate rotational speed with impact force. At lower speeds, the impact mechanism may be deactivated or significantly reduced. As the rotational speed increases (with the corresponding increase in pressure applied by the user), the impact mechanism receives sufficient energy to activate and deliver full hammering power. This interdependence is intentional, improving control and efficiency. Applying firm pressure increases rotational speed and, in turn, triggers the stronger hammering action.
4. Drill Bit and Material Interaction</h3>
The type of drill bit and the material being drilled into significantly influence the activation of the hammering mechanism. When drilling into softer materials like wood, the drill might not require the hammering action at all, and the rotational function alone may be sufficient. Conversely, when drilling into dense materials like concrete, the resistance increases, and the drill requires more pressure to initiate the hammering to aid penetration. The increased resistance, coupled with the user applying more force, facilitates the activation of the hammer mechanism.
Troubleshooting Hammer Drill Activation Issues
If you find your hammer drill consistently requires excessive pressure before hammering, some troubleshooting is in order:
1. Check the Hammer Drill's Settings
Ensure the hammer drill is set to the correct mode. Many models have a selector switch or button to engage the hammering function. Some might even have multiple hammer settings, ranging from light to heavy impacts. Double-checking this is a fundamental troubleshooting step.
2. Inspect the Drill Bit
A dull or damaged drill bit can increase resistance and impede the activation of the hammer mechanism. A worn-out or improperly sized bit may not penetrate the material effectively, requiring extra pressure. Replace the drill bit with a sharp, correctly sized bit for the material being worked on. Using the right bit for the job is crucial for both safety and efficiency.
3. Assess the Material's Hardness
The material you're drilling into plays a crucial role. Harder materials such as concrete require significantly more pressure to activate the hammering function, whereas softer materials like wood might not necessitate the hammering action at all. Using an appropriate drill bit for the material is essential. Consider pre-drilling pilot holes in tougher materials to reduce initial resistance.
4. Examine the Chuck and Bit Connection</h3>
A loose chuck or an improperly secured drill bit can lead to slippage and inadequate power transmission, hindering the activation of the hammer mechanism. Ensure the drill bit is tightly clamped in the chuck. If the chuck itself is loose, it may need tightening or replacement.
5. Lubrication and Maintenance</h3>
Regular lubrication of the drill's internal components is vital for smooth operation. Refer to your user manual for recommendations on lubrication type and frequency. A well-lubricated hammer drill will function more smoothly, requiring less pressure to activate the hammering mechanism. Neglecting lubrication can lead to increased friction and resistance.
6. Power Supply Issues (for Cordless Drills)
For cordless hammer drills, a low battery charge can limit power output, delaying or preventing the activation of the hammering function. Make sure the battery is fully charged or replace it with a fresh battery. Low battery power can mimic other problems, so this is a crucial check.
Preventative Maintenance for Optimal Performance
Regular maintenance is key to preventing issues with hammer drill activation and ensuring longevity. Here's what you can do:
1. Cleaning the Hammer Drill
After each use, clean the drill's exterior and vents to remove dust and debris. This will prevent accumulation of material that could affect performance.
2. Regular Inspection
Periodically inspect the drill's chuck, bit, and other visible parts for any signs of wear or damage. Address any issues promptly.
3. Lubrication Schedule
Adhere to the manufacturer's recommended lubrication schedule. This will keep the internal mechanisms running smoothly.
4. Correct Storage
Store the drill in a clean, dry place to prevent corrosion and damage.
Beyond the Mechanics: User Technique and Safety
While mechanical issues can cause delayed hammer activation, user technique significantly impacts the process.
1. Applying Consistent Pressure
Apply steady and consistent pressure to the drill bit. Jerky or uneven pressure can interfere with the hammer mechanism's activation. Maintain a firm grip and allow the drill to do the work. Avoid excessive force, which can damage the drill or cause injury.
2. Correct Posture and Grip
Maintain proper posture to reduce strain and ensure controlled pressure application. A firm grip ensures consistent power transfer to the drill bit.
3. Starting Slowly
Begin drilling at lower speeds and gradually increase as needed. This allows the drill to build momentum and engage the hammering mechanism more smoothly.
4. Safety Precautions
Always wear appropriate safety gear, including safety glasses and gloves, when operating a hammer drill. Never force the drill; doing so could lead to injury or damage the tool.
Conclusion: A Well-Maintained Tool is a Happy Tool
Understanding the reasons behind delayed hammer activation in most hammer drills is crucial for effective use and maintenance. By addressing potential mechanical issues, ensuring correct user technique, and performing regular maintenance, you can maximize the performance and longevity of your hammer drill. Remember, a well-maintained tool is not only more efficient but also safer to use. Following the guidelines outlined above will help you troubleshoot problems, improve your drilling experience, and ensure your hammer drill operates reliably for years to come.
Latest Posts
Latest Posts
-
The Writing Process Consists Of Gcu
Apr 02, 2025
-
Which Is An Identifying Characteristic Of Acrylic Plastics
Apr 02, 2025
-
Match Each Description With The Appropriate Step In Enzyme Catalysis
Apr 02, 2025
-
Unit 7 Right Triangles And Trigonometry Homework 4 Answers Key
Apr 02, 2025
-
Ap English Language And Composition Section 1 Answer Key
Apr 02, 2025
Related Post
Thank you for visiting our website which covers about Most Hammer Drills Will Not Hammer Until Pressure Is . We hope the information provided has been useful to you. Feel free to contact us if you have any questions or need further assistance. See you next time and don't miss to bookmark.