Overhead Includes Both Manufacturing And Nonmanufacturing Costs Under
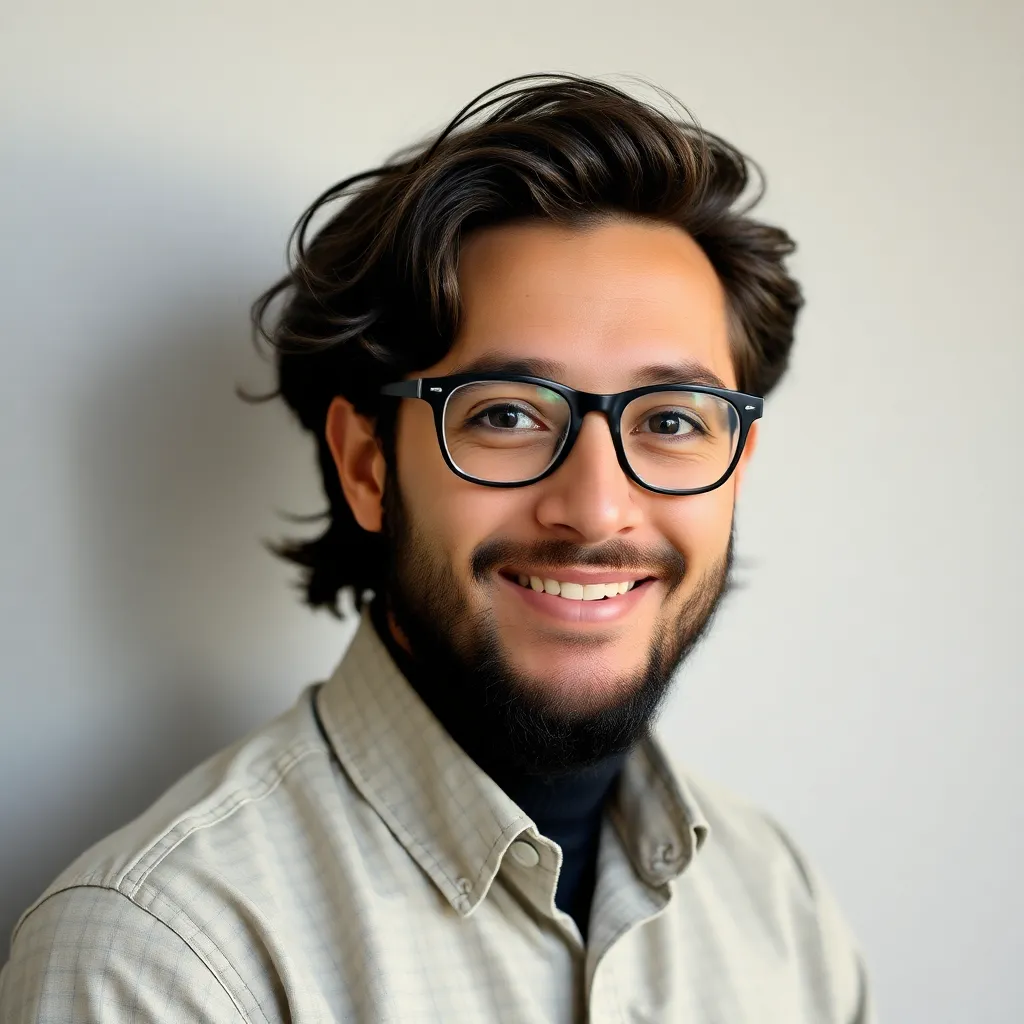
Onlines
May 08, 2025 · 6 min read

Table of Contents
Overhead: A Deep Dive into Manufacturing and Non-Manufacturing Costs
Understanding overhead costs is crucial for businesses of all sizes, regardless of industry. These costs, which are indirect expenses not directly tied to production or service delivery, significantly impact profitability and operational efficiency. This comprehensive guide delves into the multifaceted world of overhead, exploring its two primary categories: manufacturing overhead and non-manufacturing overhead. We will examine their components, how they are allocated, and their importance in financial reporting and strategic decision-making.
What is Overhead?
Overhead, also known as indirect costs, represents all expenses incurred by a business that are not directly attributable to creating a specific product or service. Unlike direct costs, such as raw materials or direct labor, overhead costs are shared across various activities and products. Accurate accounting and allocation of overhead are critical for determining product profitability, pricing strategies, and overall business performance. Failing to properly account for overhead can lead to inaccurate cost estimates, flawed pricing models, and ultimately, financial losses.
Manufacturing Overhead: The Backbone of Production
Manufacturing overhead encompasses all indirect costs associated with the production process. These costs support the creation of goods but are not directly traceable to a single unit. Understanding these costs is vital for manufacturers aiming to optimize efficiency and profitability.
Key Components of Manufacturing Overhead:
-
Indirect Labor: This includes the wages and salaries of employees who don't directly work on the product but support the manufacturing process. Examples include supervisors, maintenance personnel, quality control inspectors, and factory cleaners.
-
Indirect Materials: These are materials consumed during manufacturing but are not directly incorporated into the finished product. Examples include lubricants, cleaning supplies, and small tools that wear out over time.
-
Factory Rent and Utilities: Costs associated with the factory space, including rent, electricity, water, and heating/cooling.
-
Depreciation on Factory Equipment: The allocation of the cost of machinery and equipment over their useful life. This reflects the wear and tear of the assets used in production.
-
Factory Insurance: Premiums paid for insurance coverage protecting the factory, equipment, and employees from potential risks.
-
Factory Property Taxes: Taxes levied on the factory building and land.
-
Maintenance and Repairs: Costs incurred for maintaining and repairing factory equipment and facilities.
-
Factory Supplies: Consumables used in the manufacturing process, such as stationery, cleaning supplies, and small tools.
Allocating Manufacturing Overhead:
Accurately allocating manufacturing overhead is crucial for determining the true cost of each product. Common methods include:
-
Predetermined Overhead Rate: This involves estimating total manufacturing overhead costs for a specific period and dividing them by an estimated activity base (e.g., direct labor hours, machine hours). The resulting rate is then applied to actual production to allocate overhead costs. This method is popular for its simplicity and ability to provide timely cost information.
-
Activity-Based Costing (ABC): ABC assigns overhead costs based on the specific activities that consume those resources. This method provides a more accurate picture of overhead costs, particularly in complex manufacturing environments with multiple products and processes. However, it requires a significant upfront investment in data collection and analysis.
Non-Manufacturing Overhead: Supporting the Entire Organization
Non-manufacturing overhead, also known as administrative overhead or selling, general, and administrative (SG&A) expenses, encompasses all indirect costs not directly related to production. These costs support the overall operations and administration of the business.
Key Components of Non-Manufacturing Overhead:
-
Salaries of Administrative Staff: Wages and salaries of employees in administrative roles, such as executives, accountants, and human resources personnel.
-
Office Rent and Utilities: Costs associated with office space, including rent, electricity, water, and heating/cooling.
-
Office Supplies and Expenses: Costs of stationery, printing, postage, and other office consumables.
-
Legal and Professional Fees: Fees paid for legal services, consulting, and other professional advice.
-
Marketing and Advertising Expenses: Costs associated with promoting products or services, including advertising, public relations, and market research.
-
Research and Development Costs (R&D): Expenses incurred in developing new products or improving existing ones. While related to production indirectly, these costs are usually treated separately from manufacturing overhead.
-
Sales Commissions and Salaries: Costs related to sales activities, including salaries, commissions, and travel expenses of sales personnel. These are often categorized separately from administrative overhead.
-
Insurance (Non-Factory): Insurance premiums for general business liability, property insurance (excluding factory), and other non-factory-related insurance.
-
Depreciation on Office Equipment: Allocation of the cost of office equipment over its useful life.
-
Travel and Entertainment Expenses: Costs associated with business travel and client entertainment.
Allocating Non-Manufacturing Overhead:
Allocating non-manufacturing overhead is often less precise than allocating manufacturing overhead. Common methods include:
-
Direct Allocation: Assigning overhead costs directly to specific departments or product lines based on a reasonable measure of consumption. For example, marketing expenses might be directly allocated to specific product lines.
-
Percentage of Sales Method: Allocating overhead based on a percentage of sales revenue. This is a simple method but may not accurately reflect the true consumption of overhead resources by different segments of the business.
-
Activity-Based Costing (ABC): As with manufacturing overhead, ABC can be applied to non-manufacturing overhead to provide a more accurate allocation based on the specific activities consuming resources.
The Importance of Accurate Overhead Allocation
Accurate allocation of both manufacturing and non-manufacturing overhead is essential for several reasons:
-
Product Costing: Accurate product costs are crucial for setting profitable prices, evaluating product profitability, and making informed pricing decisions. Misallocating overhead can lead to underpricing or overpricing products.
-
Performance Evaluation: Proper overhead allocation enables more accurate evaluation of departmental performance and helps identify areas for improvement.
-
Strategic Decision-Making: Understanding overhead costs helps in making strategic decisions, such as choosing between different manufacturing processes or investment opportunities.
-
Financial Reporting: Accurate overhead allocation is required for compliance with generally accepted accounting principles (GAAP) and for preparing accurate financial statements.
-
Cost Control: Tracking and analyzing overhead costs helps identify opportunities to reduce unnecessary expenses and improve efficiency.
Overhead and Profitability: A Close Relationship
Overhead costs directly impact a company's profitability. High overhead costs can significantly reduce profit margins, even with high sales volume. Effective cost management strategies, including streamlining processes, negotiating better supplier contracts, and optimizing resource utilization, are vital for maintaining profitability. Analyzing the various components of overhead helps in identifying areas for cost reduction without compromising the quality of products or services. Continuously monitoring and controlling overhead costs is crucial for long-term business sustainability.
Conclusion: Mastering Overhead for Business Success
Overhead costs, encompassing both manufacturing and non-manufacturing components, are an integral part of any business operation. Accurate accounting, allocation, and analysis of these indirect costs are essential for informed decision-making, effective cost management, and ultimately, improved profitability. By understanding the different components of overhead and implementing appropriate allocation methods, businesses can gain a clearer picture of their true costs, enhance operational efficiency, and strengthen their competitive position in the marketplace. Regular review and optimization of overhead spending should be a cornerstone of any robust business strategy. Ignoring or mismanaging overhead can have significant and lasting negative consequences on a company's financial health and long-term success.
Latest Posts
Latest Posts
-
The Voltage Across A 10 Ohm Resistor Carrying 5a Is
May 08, 2025
-
Based On The Competing Values Framework Wells Fargo
May 08, 2025
-
Which Of The Following Is An Absolute Pathname
May 08, 2025
-
2019 Practice Exam Ap Calc Ab
May 08, 2025
-
Indicate Three Items That Describe Glycogen
May 08, 2025
Related Post
Thank you for visiting our website which covers about Overhead Includes Both Manufacturing And Nonmanufacturing Costs Under . We hope the information provided has been useful to you. Feel free to contact us if you have any questions or need further assistance. See you next time and don't miss to bookmark.