Tabletop Equipment On Legs Requires A Clearance Of At Least
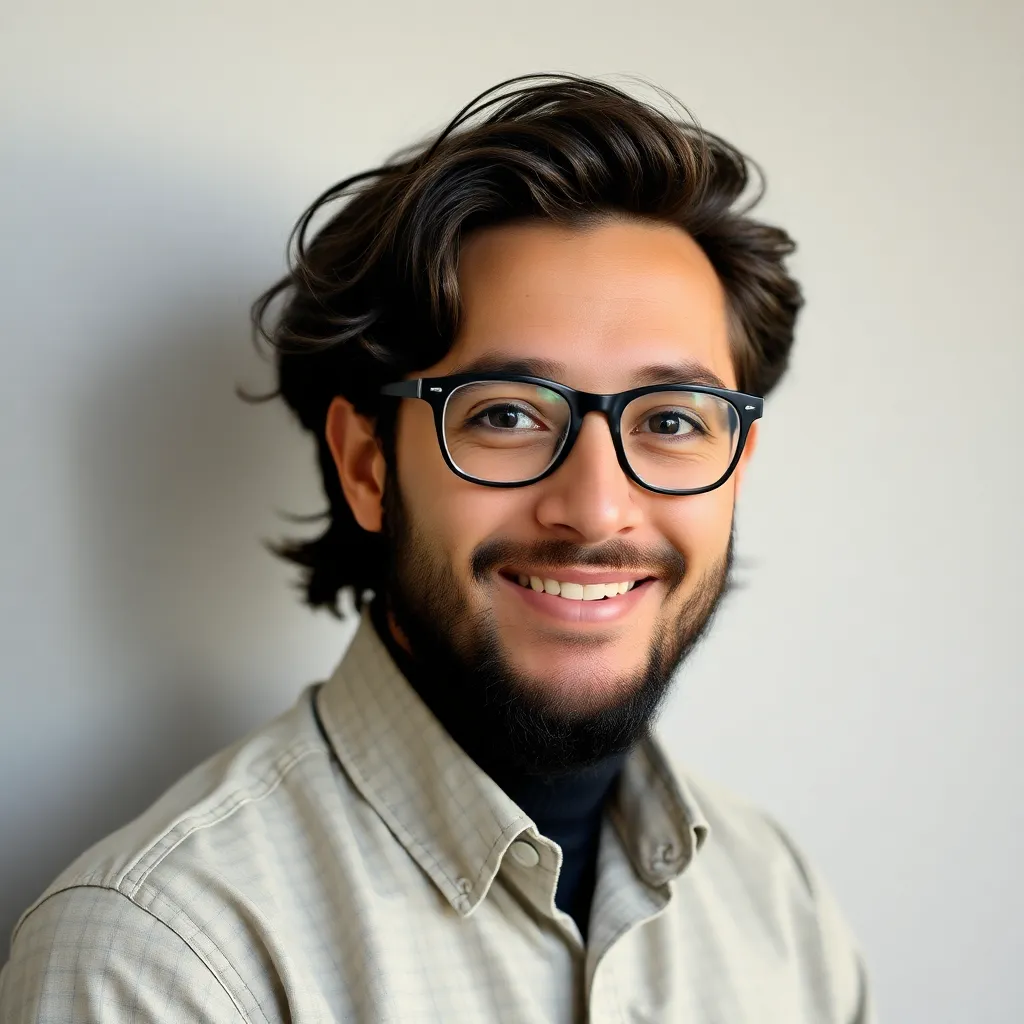
Onlines
Mar 18, 2025 · 5 min read
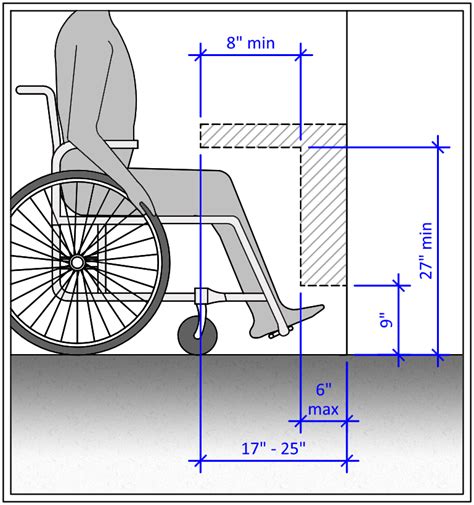
Table of Contents
Tabletop Equipment on Legs: Minimum Clearance Requirements for Safety and Efficiency
Tabletop equipment, from laboratory instruments to industrial machinery, often sits on legs or stands. Ensuring adequate clearance around this equipment is crucial for safety, efficient operation, and compliance with various regulations. This article delves into the factors determining the necessary clearance, focusing on safety regulations, operational needs, and best practices for different types of equipment and environments.
Understanding the Importance of Clearance
The minimum clearance required around tabletop equipment on legs isn't a single, universally applicable number. It's a dynamic calculation influenced by several interconnected factors. Insufficient clearance can lead to a range of problems, including:
-
Safety Hazards: Tripping hazards are the most immediate concern. Cluttered spaces around equipment increase the risk of accidents, potentially causing injuries to personnel. Furthermore, inadequate clearance can hinder quick escapes in case of emergencies, such as fires or equipment malfunctions. This is particularly critical in laboratories and industrial settings.
-
Operational Inefficiencies: Restricted access makes routine tasks like maintenance, cleaning, and adjustments more difficult and time-consuming. This can lead to delays in production and increased downtime.
-
Equipment Damage: Improper clearance can increase the risk of accidental damage to the equipment itself, especially delicate instruments. Collisions with surrounding objects or people can lead to malfunction or even total destruction.
-
Compliance Issues: Many industries and regulatory bodies have specific requirements regarding workspace clearance. Failure to meet these standards can result in fines, legal liabilities, and reputational damage.
Factors Determining Minimum Clearance
Several key factors influence the minimum clearance needed around tabletop equipment:
1. Equipment Size and Dimensions:
The physical dimensions of the equipment itself are paramount. Larger, bulkier equipment naturally necessitates more clearance. This includes the width, depth, and height of the equipment, as well as any protruding parts like knobs, handles, or power cords.
2. Accessibility Needs:
Consider how often the equipment needs access for maintenance, repair, or cleaning. Equipment requiring frequent access needs significantly more clearance than equipment used infrequently. Think about the space needed for technicians to work comfortably and safely.
3. Traffic Patterns and Workspace Layout:
The flow of people and materials in the workspace is critical. High-traffic areas demand more clearance to prevent collisions and maintain safe passage. Consider the proximity of other equipment and obstacles. Strategic placement of equipment to minimize traffic conflicts is essential.
4. Type of Equipment and its Operational Requirements:
Different types of equipment have different operational needs. For example, laboratory equipment often requires additional clearance for handling samples, reagents, and waste disposal. Industrial machinery might need more space for material handling and safety mechanisms.
5. Safety Regulations and Industry Standards:
Industry-specific safety regulations often dictate minimum clearance requirements. Organizations like OSHA (Occupational Safety and Health Administration) in the US, or equivalent bodies in other countries, provide guidelines to minimize workplace hazards. These standards frequently mandate specific distances for aisles, walkways, and access to equipment.
6. Ergonomics and User Comfort:
Proper clearance contributes significantly to ergonomic design. Sufficient space around equipment allows users to work comfortably and avoid awkward postures that can cause musculoskeletal disorders. This is particularly important for tasks requiring prolonged periods of operation.
Recommended Clearance Guidelines
While precise measurements depend on the specific circumstances, some general guidelines can be helpful:
-
Minimum Aisles and Walkways: OSHA generally recommends a minimum of 36 inches (91.44 cm) for main aisles and walkways, and at least 28 inches (71.12 cm) for narrower aisles. However, wider clearances are strongly preferred for safety and efficiency, especially in busy environments.
-
Clearance Around Equipment: As a general rule, allow at least 24 inches (61 cm) of clearance on all sides of tabletop equipment on legs. This allows for comfortable access and movement around the equipment. For larger or more complex equipment, this distance should be increased significantly.
-
Overhead Clearance: Consider the height of the equipment and the potential for overhead obstructions. Sufficient overhead clearance is essential to prevent head injuries.
-
Emergency Access: Ensure that pathways remain clear in case of emergencies, allowing for quick and safe evacuation.
Best Practices for Maintaining Adequate Clearance
-
Regular Audits and Inspections: Conduct regular inspections of the workspace to identify and address any clearance issues.
-
Proper Equipment Placement: Carefully plan the location of equipment to optimize workflow and minimize congestion.
-
Clear Signage and Markings: Use clear signage to indicate restricted areas or zones with limited clearance.
-
Training and Education: Train personnel on safe work practices and the importance of maintaining adequate clearance around equipment.
-
Storage Solutions: Implement efficient storage solutions to prevent clutter and maintain clear pathways.
-
Regular Cleaning and Maintenance: Regularly clean and maintain equipment to prevent obstructions and hazards.
Case Studies: Clearance Requirements in Different Settings
The clearance requirements vary significantly depending on the specific environment.
1. Laboratory Settings:
Laboratory environments often handle hazardous materials and delicate equipment. Increased clearance is needed around fume hoods, centrifuges, and other specialized instruments. Safe handling of chemicals and waste demands extra space for maneuvering and minimizing the risk of spills or accidents.
2. Industrial Settings:
Industrial settings involve heavier machinery and higher traffic volume. Wider aisles and more significant clearance around equipment are necessary to prevent collisions and injuries. Maintenance access might necessitate even greater clearances.
3. Healthcare Settings:
Healthcare facilities require appropriate clearance to allow for easy access to patients and equipment. Clear pathways are crucial for efficient movement of medical personnel and equipment during emergencies.
4. Office Settings:
Even in office settings, proper clearance around desks, printers, and other equipment is important for smooth workflow and comfortable working conditions.
Conclusion: Prioritizing Safety and Efficiency Through Proper Clearance
Ensuring adequate clearance around tabletop equipment on legs is not just a matter of convenience; it's a critical safety precaution and a fundamental aspect of efficient workspace design. By understanding the factors influencing minimum clearance requirements, adopting best practices, and adhering to relevant safety regulations, organizations can create safer, more productive, and compliant work environments. Remember, prioritizing safety and efficiency through proper clearance is an investment in the well-being of personnel and the success of any operation. Regularly reassess your workspace layout and equipment placement to ensure ongoing compliance and a safe working environment for everyone.
Latest Posts
Latest Posts
-
Code Standards And Practices 3 Lesson 1
Mar 18, 2025
-
Mr Barker Enjoys A Comfortable Retirement Income
Mar 18, 2025
-
Afterlife The Strange Science Of Decay Answer Key
Mar 18, 2025
-
Unit 3 Progress Check Frq Part A Ap Calculus
Mar 18, 2025
-
A Long Way Gone Chapter Notes
Mar 18, 2025
Related Post
Thank you for visiting our website which covers about Tabletop Equipment On Legs Requires A Clearance Of At Least . We hope the information provided has been useful to you. Feel free to contact us if you have any questions or need further assistance. See you next time and don't miss to bookmark.