The Amount Of Inspection Needed Depends On __________ And __________.
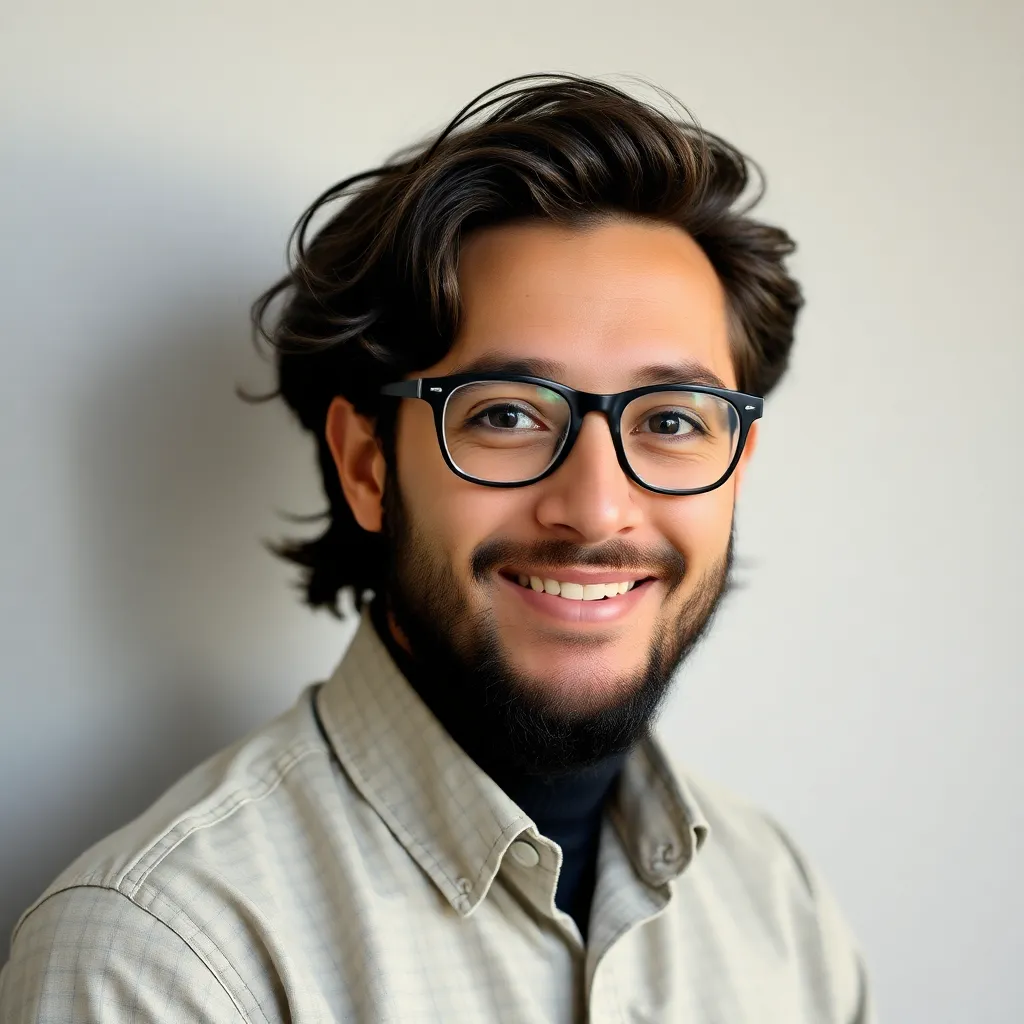
Onlines
Apr 04, 2025 · 6 min read

Table of Contents
The Amount of Inspection Needed Depends on Risk and Context
The amount of inspection required for any given process, product, or system isn't a fixed quantity. It's a dynamic variable heavily influenced by two crucial factors: risk and context. Understanding and effectively balancing these elements is essential for creating efficient and effective inspection programs that ensure quality without unnecessary overhead. Let's delve deeper into how risk and context determine inspection needs.
Risk Assessment: The Cornerstone of Inspection Planning
At the heart of determining inspection intensity lies a thorough risk assessment. This involves identifying potential hazards, evaluating their likelihood of occurrence, and assessing the severity of their consequences if they materialize. This forms the basis for a prioritized approach to inspection, focusing resources where they're most needed.
Identifying Potential Hazards: A Comprehensive Approach
Identifying hazards requires a multi-faceted approach, encompassing:
- Process analysis: Scrutinizing the entire process flow, from raw material to finished product, pinpointing potential points of failure or defect introduction. This includes analyzing equipment capabilities, human error possibilities, and environmental factors.
- Product characteristics: Examining the product itself, identifying critical parameters and potential vulnerabilities. This involves understanding the product's intended use, target market, and potential risks associated with its failure.
- Historical data: Analyzing past performance data – defect rates, customer complaints, and incident reports – to identify recurring issues and potential weaknesses. This data provides valuable insight into areas requiring increased scrutiny.
- Regulatory compliance: Considering all relevant regulations, standards, and legal requirements that apply to the product or process. This ensures adherence to mandatory inspection protocols and minimizes potential legal liabilities.
- Stakeholder input: Consulting with various stakeholders, including engineers, operators, quality control personnel, and even customers, to gather diverse perspectives and identify potential hazards that might otherwise be overlooked.
Evaluating Likelihood and Severity: The Risk Matrix
Once hazards are identified, the next step is to evaluate their likelihood of occurrence and the severity of their consequences using a risk matrix. This matrix typically employs a scoring system, assigning numerical values to both likelihood and severity, which are then multiplied to determine an overall risk score. Higher scores indicate higher-risk areas demanding more stringent inspection.
Example Risk Matrix:
Likelihood | Severity | Risk Score | Inspection Intensity |
---|---|---|---|
Low (1) | Low (1) | 1 | Minimal |
Low (1) | Medium (3) | 3 | Moderate |
Low (1) | High (5) | 5 | High |
Medium (3) | Low (1) | 3 | Moderate |
Medium (3) | Medium (3) | 9 | Very High |
Medium (3) | High (5) | 15 | Critical |
High (5) | Low (1) | 5 | High |
High (5) | Medium (3) | 15 | Critical |
High (5) | High (5) | 25 | Immediate Action Required |
This matrix provides a clear framework for prioritizing inspection efforts, allocating resources effectively to address the most critical risks.
Implementing Risk-Based Inspection: A Practical Approach
Based on the risk assessment, an inspection plan can be developed, outlining the frequency, methods, and extent of inspection for each identified hazard. This might include:
- Increased sampling frequency: For high-risk areas, a higher sampling frequency ensures greater coverage and earlier detection of potential defects.
- More stringent testing methods: Employing more rigorous testing techniques, such as destructive testing or specialized analysis, for critical parameters.
- Dedicated inspection personnel: Assigning experienced and well-trained inspectors to high-risk areas.
- Process improvements: Implementing process modifications to mitigate identified hazards and reduce the risk of defects.
Contextual Factors: Tailoring Inspection to Specific Needs
While risk assessment forms the foundation of inspection planning, contextual factors add another layer of complexity and nuance. These factors significantly influence the type and amount of inspection needed.
Industry Regulations and Standards: Legal Compliance
Different industries have unique regulatory landscapes and standards that dictate inspection requirements. For instance, the pharmaceutical industry has exceptionally stringent quality control standards, leading to more intensive inspection procedures compared to, say, the furniture industry. Adherence to these standards is not merely a best practice; it's a legal necessity.
Production Volume and Capacity: Scaling Inspection
Production volume significantly impacts inspection needs. High-volume manufacturing operations might require automated inspection systems and statistical sampling methods to ensure efficient quality control without halting production. Low-volume, bespoke manufacturing might utilize more comprehensive, manual inspections.
Product Complexity: Assessing Critical Parameters
Complex products with numerous components and intricate functionalities demand more thorough inspections. This includes not just visual inspections but also detailed functional tests and performance evaluations. Simple products, conversely, require less extensive inspection.
Customer Expectations and Brand Reputation: Meeting Market Demands
Customer expectations and brand reputation are crucial contextual factors. Companies with a strong focus on quality and customer satisfaction might opt for more extensive inspections to ensure products meet or exceed customer expectations. This proactive approach helps build trust and enhance brand reputation.
Technological Advancements: Integrating Automation and AI
Advances in technology, such as automated inspection systems, AI-powered defect detection, and advanced analytics, significantly impact inspection strategies. These technologies can enhance efficiency, accuracy, and cost-effectiveness, allowing for more comprehensive inspections in less time.
Balancing Risk and Context: Achieving Optimal Inspection
The optimal amount of inspection is achieved by carefully balancing the identified risks with the contextual factors. It’s not about simply maximizing inspection; it's about achieving the right level of inspection to ensure quality and safety without unnecessary costs or delays.
Optimizing Inspection Processes: Strategies for Efficiency
Several strategies can help optimize inspection processes and ensure efficient resource allocation:
- Statistical process control (SPC): Using statistical methods to monitor and control process variations, reducing the need for excessive inspections.
- Automated inspection systems: Implementing automated systems to handle high-volume inspections, enhancing speed and accuracy.
- Data-driven decision-making: Using data analytics to identify trends, patterns, and anomalies, allowing for targeted inspections.
- Continuous improvement: Regularly reviewing and refining inspection processes based on feedback, data analysis, and best practices.
Conclusion: A Holistic Approach to Inspection Planning
The amount of inspection needed is not a one-size-fits-all answer. It's a dynamic variable determined by a careful consideration of both risk and context. By implementing a comprehensive risk assessment framework, understanding the contextual factors influencing inspection needs, and employing efficient inspection strategies, organizations can establish effective quality control systems that ensure product safety, customer satisfaction, and operational efficiency. Remember, the goal is not to simply do inspections, but to do the right inspections, achieving the optimal balance between thoroughness and efficiency. This holistic approach minimizes waste, maximizes resource utilization, and ultimately contributes to a more robust and resilient organization.
Latest Posts
Latest Posts
-
Which Of The Following Best Defines The Asch Effect
Apr 12, 2025
-
A Supervisor Set The Following Performance Goal For New Employees
Apr 12, 2025
-
Consumer Mathematics Workbook Activity Answer Key Pdf
Apr 12, 2025
-
A Legal Query Must Be Written Using
Apr 12, 2025
-
Select The True Statements About The Process Of Learning Ai
Apr 12, 2025
Related Post
Thank you for visiting our website which covers about The Amount Of Inspection Needed Depends On __________ And __________. . We hope the information provided has been useful to you. Feel free to contact us if you have any questions or need further assistance. See you next time and don't miss to bookmark.