The Number Of Accidents At A Manufacturing Facility
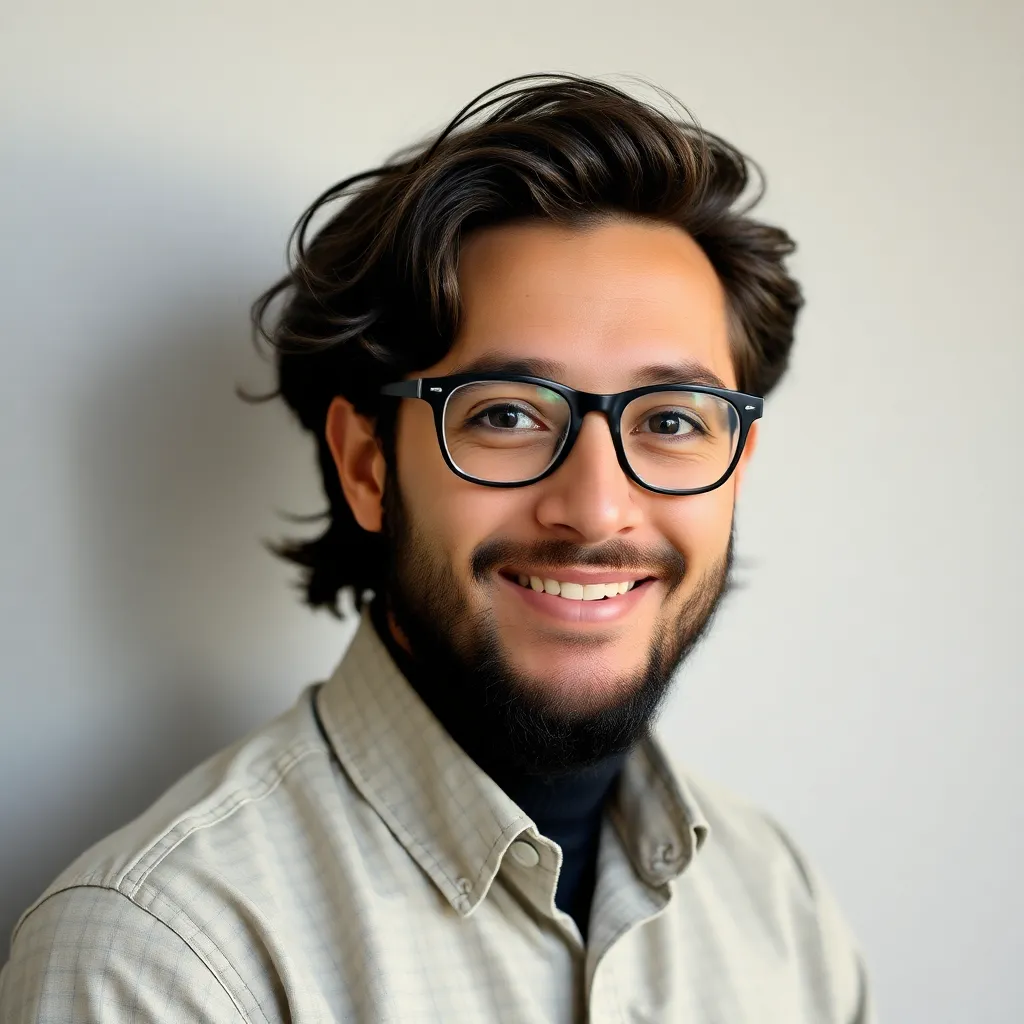
Onlines
Mar 20, 2025 · 7 min read
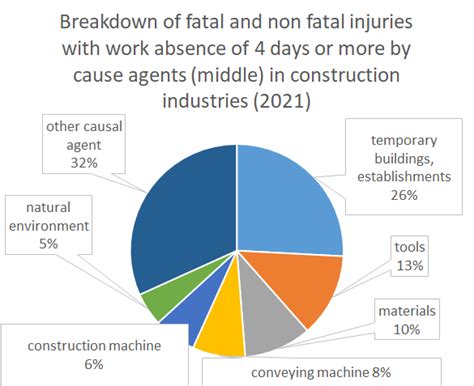
Table of Contents
The Number of Accidents at a Manufacturing Facility: A Comprehensive Analysis
The number of accidents at a manufacturing facility is a critical indicator of workplace safety and operational efficiency. High accident rates translate to increased costs, decreased productivity, legal liabilities, and, most importantly, human suffering. This comprehensive analysis delves into the various factors contributing to accidents in manufacturing settings, explores effective strategies for prevention, and discusses the importance of data-driven safety management.
Understanding the Scope of the Problem: Accident Statistics in Manufacturing
Accidents in manufacturing facilities encompass a wide range of incidents, from minor injuries to fatalities. These can include:
- Slips, trips, and falls: These account for a significant portion of workplace accidents, often resulting from cluttered workspaces, inadequate lighting, or slippery surfaces.
- Machine-related injuries: Contact with moving machinery, entanglement, or caught-in hazards are common causes of serious injuries in manufacturing.
- Struck-by incidents: Objects falling from heights, colliding vehicles, or moving equipment can cause significant injuries.
- Caught-in/between incidents: Workers becoming trapped or crushed between equipment or objects.
- Exposure to hazardous substances: Contact with chemicals, fumes, or other harmful substances can lead to a range of health issues.
- Fire and explosions: Flammable materials and equipment pose a significant fire risk in manufacturing settings.
While precise global statistics are challenging to compile due to variations in reporting standards and data accessibility, numerous studies consistently demonstrate that manufacturing remains a high-risk industry. The number of accidents varies significantly depending on factors such as the specific industry sector (e.g., food processing versus heavy machinery), company size, and the effectiveness of safety programs. Understanding your specific facility's accident rates is paramount.
Analyzing Accident Data: Identifying Trends and Patterns
Effective accident prevention requires a thorough understanding of accident patterns within a specific manufacturing facility. This involves:
- Data collection: Implement a robust system for recording and categorizing all accidents, no matter how minor. This should include details such as the date, time, location, nature of the injury, contributing factors, and any witnesses.
- Data analysis: Use statistical methods to identify trends and patterns in accidents. Are there specific machines, work areas, or times of day that are associated with a higher frequency of accidents? Are certain types of injuries more prevalent?
- Root cause analysis: Don't just address the symptoms; delve into the underlying causes of accidents. Tools like the "5 Whys" technique or fishbone diagrams can be invaluable in uncovering root causes.
Identifying trends enables proactive measures. For example, if slips and trips are frequently occurring in a particular area, improving lighting, addressing floor maintenance, and implementing slip-resistant footwear policies can significantly reduce the risk. If machine-related injuries are prominent, investigating machine guarding, operator training, and lockout/tagout procedures is essential.
Key Contributing Factors to Manufacturing Accidents
A multitude of factors contribute to accidents in manufacturing settings. Understanding these factors is crucial for developing effective prevention strategies. These can be broadly categorized as:
1. Human Factors:
- Lack of training: Inadequate training on safe operating procedures, hazard recognition, and emergency response can lead to accidents.
- Fatigue and stress: Long working hours, excessive workload, and poor work-life balance can impair judgment and increase the risk of errors.
- Complacency and risk-taking: Familiarity with hazardous tasks can lead to a false sense of security and risky behavior.
- Poor communication: Ineffective communication between workers, supervisors, and management can result in misunderstandings and accidents.
- Human error: Even with adequate training and precautions, human error remains a significant contributing factor.
2. Environmental Factors:
- Poor housekeeping: Cluttered workspaces, spills, and inadequate lighting increase the risk of slips, trips, and falls.
- Inadequate ventilation: Poor ventilation can lead to exposure to harmful fumes and dust.
- Extreme temperatures: Working in excessively hot or cold environments can lead to fatigue and increase the risk of accidents.
- Noise pollution: High noise levels can impair hearing and distract workers, increasing the risk of accidents.
3. Equipment and Machinery Factors:
- Outdated or poorly maintained equipment: Malfunctioning machinery increases the risk of accidents.
- Inadequate machine guarding: Insufficient safety guards on machinery expose workers to hazards.
- Lack of emergency shut-off mechanisms: Difficulties in quickly shutting down equipment in emergencies can worsen the consequences of accidents.
4. Management and Organizational Factors:
- Inadequate safety programs: Lack of comprehensive safety policies, procedures, and training programs.
- Poor safety culture: A culture that prioritizes production over safety.
- Insufficient resources for safety: Lack of funding for safety equipment, training, and inspections.
- Inadequate safety leadership: Lack of commitment from management to safety.
Strategies for Accident Prevention in Manufacturing
Preventing accidents requires a multi-faceted approach that addresses all the contributing factors mentioned above. Effective strategies include:
1. Implementing a Robust Safety Management System:
This involves establishing clear safety policies, procedures, and training programs; conducting regular safety inspections and audits; and actively investigating and analyzing all accidents. A strong safety management system should be integrated into all aspects of the manufacturing process, from design and procurement to operations and maintenance.
2. Enhancing Employee Training:
Comprehensive training programs should cover safe operating procedures, hazard recognition, emergency response, and the use of personal protective equipment (PPE). Regular refresher training is essential to reinforce safety practices and address any changes in procedures or equipment.
3. Improving Workplace Ergonomics:
Designing workstations and tasks to minimize physical strain can reduce the risk of musculoskeletal injuries. This includes ergonomic assessments, adjustments to workstations, and the use of ergonomic tools and equipment.
4. Investing in Safety Equipment and Technology:
Providing employees with appropriate PPE, installing safety guards on machinery, and utilizing advanced safety technologies can significantly reduce accident risks. Regular maintenance and inspection of safety equipment are crucial.
5. Fostering a Strong Safety Culture:
Cultivating a safety-conscious culture requires leadership commitment, employee involvement, and open communication. Regular safety meetings, safety campaigns, and recognition programs can reinforce the importance of safety. Open communication and a blame-free reporting system encourage employees to report hazards and near misses without fear of retribution.
6. Utilizing Data-Driven Safety Management:
Tracking and analyzing accident data allows for the identification of trends, patterns, and root causes of accidents. This information can then be used to target prevention efforts and improve safety performance. Technology can play a significant role here, with software solutions capable of managing safety data, automating reporting, and generating insightful reports.
7. Regular Safety Inspections and Audits:
Regular inspections and audits ensure that safety procedures are being followed, equipment is properly maintained, and hazards are identified and addressed. These inspections should be conducted by trained personnel and involve a systematic review of all aspects of the workplace.
8. Implementing Lockout/Tagout Procedures:
Lockout/tagout (LOTO) procedures are essential for preventing accidental start-up of machinery during maintenance or repair. These procedures ensure that energy sources are isolated and equipment is rendered inoperable before any work is performed. Consistent training and enforcement of LOTO procedures are critical.
9. Emergency Response Planning:
Developing and regularly practicing emergency response plans is crucial for minimizing the consequences of accidents. This includes establishing clear communication channels, designating emergency response teams, and providing appropriate training on emergency procedures.
10. Continuous Improvement:
Safety management should be an ongoing process of continuous improvement. Regularly reviewing safety performance, identifying areas for improvement, and implementing corrective actions are essential for maintaining a safe and productive workplace.
The Importance of Proactive Safety Measures: Preventing Accidents Before They Happen
Reactive measures, such as investigating accidents after they occur, are necessary but insufficient. A proactive approach focuses on preventing accidents before they happen. This requires a fundamental shift in mindset, prioritizing safety as an integral part of the manufacturing process rather than an afterthought. Proactive measures include:
- Hazard identification and risk assessment: Regularly identify and assess potential hazards in the workplace, implementing appropriate control measures to mitigate risks.
- Job hazard analysis (JHA): Systematic analysis of each job to identify potential hazards and develop safe work procedures.
- Pre-start safety checks: Performing safety checks on equipment and machinery before starting operations.
- Regular maintenance and inspections: Ensuring that equipment is properly maintained and regularly inspected to prevent malfunctions.
- Near miss reporting: Encouraging employees to report near misses, which can provide valuable insights into potential hazards before they result in accidents.
Conclusion: Building a Culture of Safety in Manufacturing
Reducing the number of accidents at a manufacturing facility is not simply a matter of compliance; it is a fundamental aspect of responsible business operations. A strong safety culture, coupled with effective safety management systems and proactive measures, is paramount. The cost of accidents – financial, reputational, and human – far outweighs the investment in robust safety programs. By prioritizing safety, manufacturing facilities can create a healthier, more productive, and more sustainable work environment for all. The data-driven approach outlined in this analysis enables continuous improvement and a journey towards a truly safe and accident-free manufacturing environment.
Latest Posts
Latest Posts
-
Which Of The Following Statements Regarding Abdominal Eviscerations Is Correct
Mar 20, 2025
-
Othello Act 2 Scene 3 Summary
Mar 20, 2025
-
9 7 Skills Practice Equations Of Circles
Mar 20, 2025
-
Summary Of The Giver Chapter 8
Mar 20, 2025
-
The Biology Of Osmosis Jones Answer Key
Mar 20, 2025
Related Post
Thank you for visiting our website which covers about The Number Of Accidents At A Manufacturing Facility . We hope the information provided has been useful to you. Feel free to contact us if you have any questions or need further assistance. See you next time and don't miss to bookmark.