The Total Manufacturing Cost Variance Consists Of
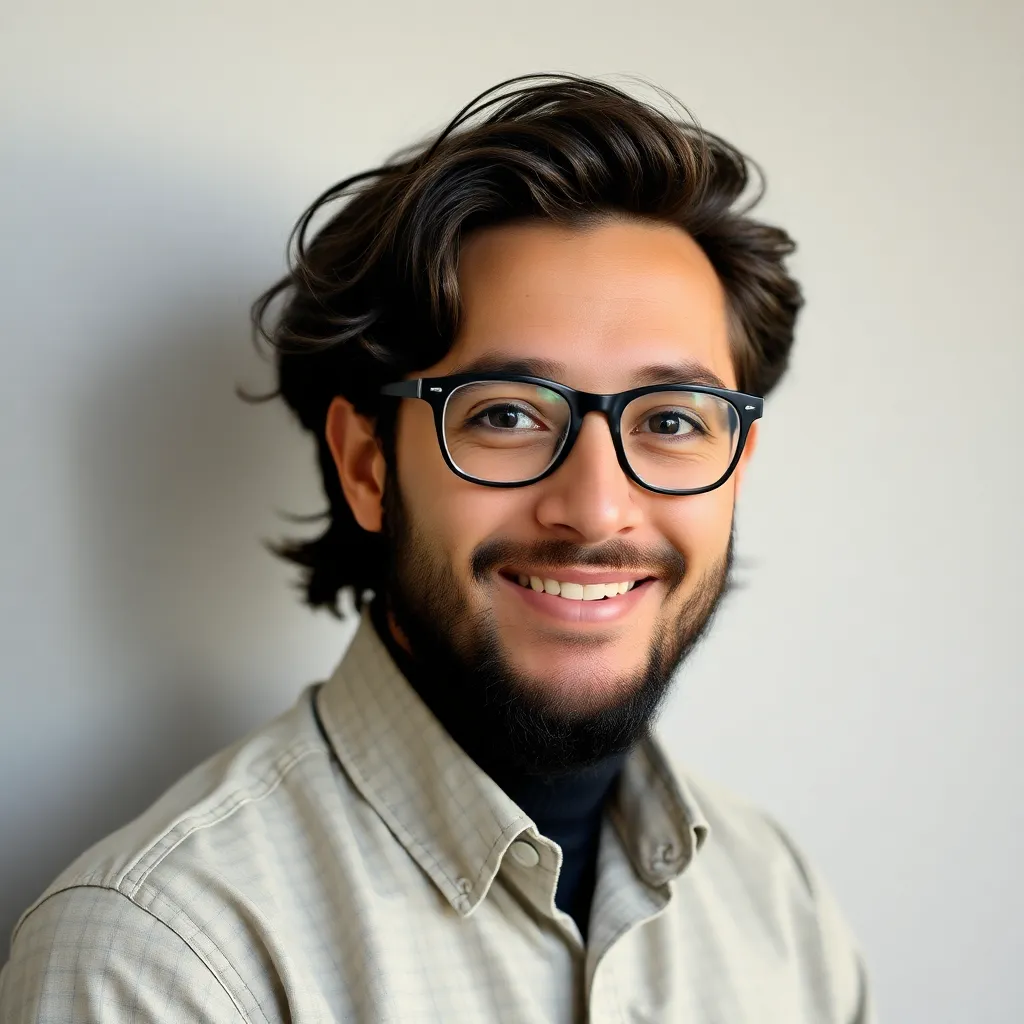
Onlines
May 12, 2025 · 6 min read
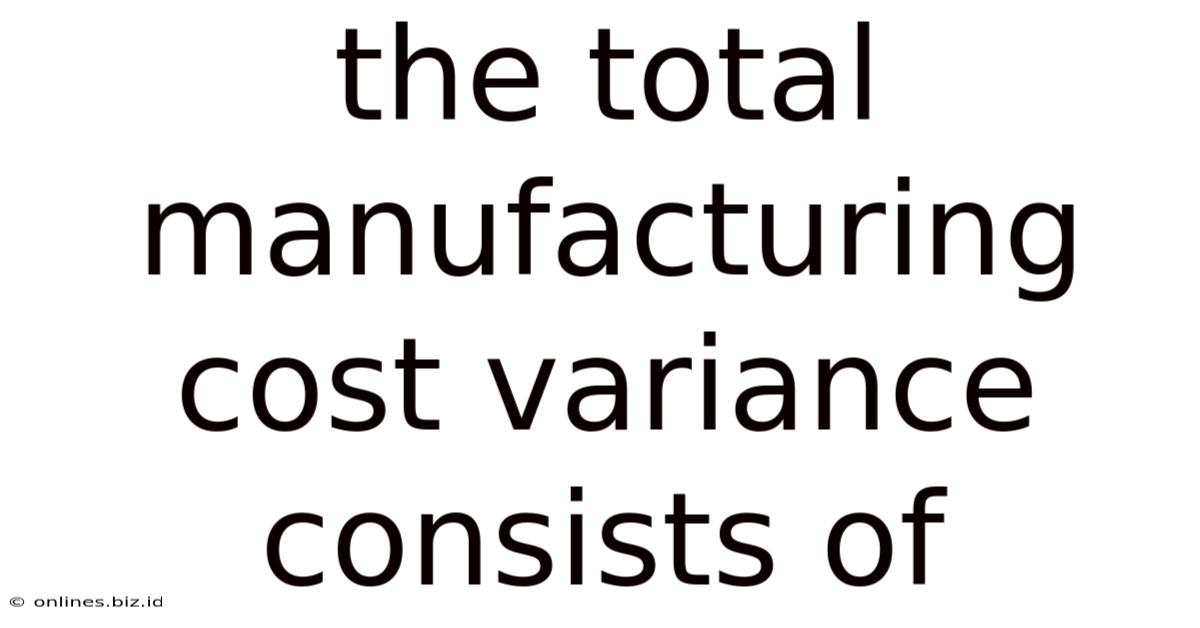
Table of Contents
The Total Manufacturing Cost Variance: A Comprehensive Guide
Understanding manufacturing costs is crucial for any business aiming for profitability and sustainable growth. A key aspect of cost management is analyzing variances – the difference between actual and planned costs. This article delves deep into the total manufacturing cost variance, exploring its components, how to calculate them, and their implications for effective decision-making. We'll also touch upon the importance of variance analysis in improving operational efficiency and ultimately boosting the bottom line.
Understanding Manufacturing Costs
Before dissecting the total manufacturing cost variance, let's establish a firm grasp on the fundamental components of manufacturing costs. These costs are broadly classified into three categories:
1. Direct Materials Costs:
These are the raw materials directly used in the production process. Examples include fabric for clothing, steel for automobiles, or flour for bread. Direct materials cost variance arises from differences between the actual cost of materials used and the standard cost. This variance can be further broken down into materials price variance (difference in actual and standard price) and materials usage variance (difference in actual and standard quantity used).
2. Direct Labor Costs:
This encompasses the wages and salaries paid to workers directly involved in the manufacturing process. Think assembly line workers, machine operators, or skilled craftspeople. The direct labor cost variance measures the difference between actual and standard direct labor costs. It's further analyzed into labor rate variance (difference in actual and standard labor rates) and labor efficiency variance (difference in actual and standard labor hours).
3. Manufacturing Overhead Costs:
These are indirect costs associated with the production process, not easily traceable to specific products. Examples include factory rent, utilities, depreciation of machinery, and indirect labor (supervisors, maintenance staff). The manufacturing overhead cost variance represents the difference between actual and budgeted overhead costs. This variance is complex and requires detailed analysis to pinpoint the sources of the deviation. It's often analyzed into variable overhead variances (related to materials or labor) and fixed overhead variances.
Deconstructing the Total Manufacturing Cost Variance
The total manufacturing cost variance is the overarching measure of the difference between the actual total manufacturing costs and the standard (or budgeted) total manufacturing costs for a given period. It's a crucial indicator of overall production efficiency and cost control. A significant positive variance (actual costs exceeding standard costs) signals potential problems requiring investigation, while a favorable negative variance (actual costs below standard costs) indicates efficient operations.
The total manufacturing cost variance is the sum of the individual variances for each cost category:
Total Manufacturing Cost Variance = Direct Materials Cost Variance + Direct Labor Cost Variance + Manufacturing Overhead Cost Variance
Detailed Analysis of Individual Variances
Let's delve deeper into the calculation and interpretation of each individual variance. Understanding these components is essential for effective variance analysis and implementing corrective actions.
1. Direct Materials Cost Variance
The Direct Materials Cost Variance (DMCV) reflects the difference between the actual cost of materials used and the standard cost of materials that should have been used for the actual production level.
DMCV = (Actual Quantity x Actual Price) – (Standard Quantity x Standard Price)
This variance can be further broken down into:
-
Materials Price Variance (MPV): This focuses solely on the difference in the price paid for materials. MPV = (Actual Quantity x (Actual Price – Standard Price)) A favorable MPV indicates that materials were purchased at a lower price than anticipated.
-
Materials Usage Variance (MUV): This assesses the efficiency of material usage. MUV = (Standard Price x (Actual Quantity – Standard Quantity)) A favorable MUV signifies that less material was used than expected for the actual output.
Understanding both MPV and MUV helps pinpoint whether cost overruns stemmed from purchasing expensive materials or inefficient usage.
2. Direct Labor Cost Variance
The Direct Labor Cost Variance (DLCV) measures the difference between the actual direct labor costs and the standard direct labor costs for the actual output.
DLCV = (Actual Hours x Actual Rate) – (Standard Hours x Standard Rate)
It's broken down into:
-
Labor Rate Variance (LRV): This variance isolates the impact of differing labor rates (wages). LRV = (Actual Hours x (Actual Rate – Standard Rate)) A favorable LRV implies that labor costs were lower than anticipated, perhaps due to negotiating better wages or employing less expensive labor.
-
Labor Efficiency Variance (LEV): This highlights the efficiency of labor utilization. LEV = (Standard Rate x (Actual Hours – Standard Hours)) A favorable LEV suggests that workers were more efficient than expected, completing the production with fewer hours.
3. Manufacturing Overhead Cost Variance
The Manufacturing Overhead Cost Variance (MOCV) represents the difference between actual and budgeted manufacturing overhead costs. This is typically the most complex variance to analyze because overhead costs comprise numerous diverse items.
MOCV = Actual Overhead Costs – Budgeted Overhead Costs
The MOCV is often further broken down into variable and fixed overhead variances.
-
Variable Overhead Variance: This variance focuses on variable overhead costs, such as indirect materials and utilities. Similar to direct costs, it can be further dissected into a variable overhead spending variance (difference between actual and budgeted variable overhead costs) and a variable overhead efficiency variance (difference between actual and budgeted variable overhead based on efficiency).
-
Fixed Overhead Variance: This variance pertains to fixed overhead costs, like rent, depreciation, and salaries of certain factory personnel. It often includes a fixed overhead budget variance (difference between actual and budgeted fixed overhead costs) and a fixed overhead volume variance (difference between budgeted fixed overhead and applied fixed overhead based on actual production). The volume variance arises because fixed overhead is often applied based on a predetermined activity level (e.g., machine hours), and discrepancies between planned and actual production affect the cost applied per unit.
Investigating and Addressing Variances
Identifying significant variances is only the first step. Effective cost management requires a thorough investigation to understand the underlying causes. This involves:
-
Data Analysis: Examine detailed production records, purchasing documents, and timekeeping data to pinpoint the root causes.
-
Interviews: Talk to employees involved in the production process to gather insights and identify operational bottlenecks.
-
Process Review: Analyze the production process for areas of improvement, waste reduction opportunities, and potential inefficiencies.
-
Corrective Actions: Based on the investigation's findings, implement appropriate corrective measures, such as improving material procurement, enhancing worker training, or streamlining production processes.
The Importance of Regular Variance Analysis
Regular variance analysis is vital for several reasons:
-
Improved Cost Control: It helps identify areas where costs are exceeding budgets, allowing for timely intervention.
-
Enhanced Operational Efficiency: By uncovering inefficiencies, variance analysis facilitates process improvements and waste reduction.
-
Better Decision-Making: The insights gained from variance analysis inform strategic decisions related to pricing, resource allocation, and investment in new technologies.
-
Increased Profitability: By improving cost control and operational efficiency, variance analysis ultimately contributes to higher profitability.
Conclusion
The total manufacturing cost variance is a powerful tool for managing costs and improving profitability in manufacturing businesses. By understanding its components—direct materials cost variance, direct labor cost variance, and manufacturing overhead cost variance—and conducting thorough investigations into unfavorable variances, businesses can pinpoint inefficiencies, implement corrective actions, and enhance their overall operational performance. Regular and rigorous variance analysis is not merely a reporting exercise; it's a crucial element of proactive cost management and strategic decision-making, paving the way for a more profitable and competitive future. Remember that the accuracy and usefulness of your variance analysis heavily depend on the accuracy and reliability of your standard costs. Regular reviews and adjustments of your standards are necessary to ensure the ongoing relevance and value of your analysis.
Latest Posts
Latest Posts
-
Steven Roberts Is A Mental Health Counselor In Oregon Npi
May 12, 2025
-
An Entrepreneur Is A Person Who A Business
May 12, 2025
-
When Deciding What Course Of Action To Follow The Nurse
May 12, 2025
-
How Does This Most Likely Make Abby Feel
May 12, 2025
-
For Any Integer X X2 X Will Always Produce
May 12, 2025
Related Post
Thank you for visiting our website which covers about The Total Manufacturing Cost Variance Consists Of . We hope the information provided has been useful to you. Feel free to contact us if you have any questions or need further assistance. See you next time and don't miss to bookmark.