Three Broad Categories Of Definitions Of Quality Are
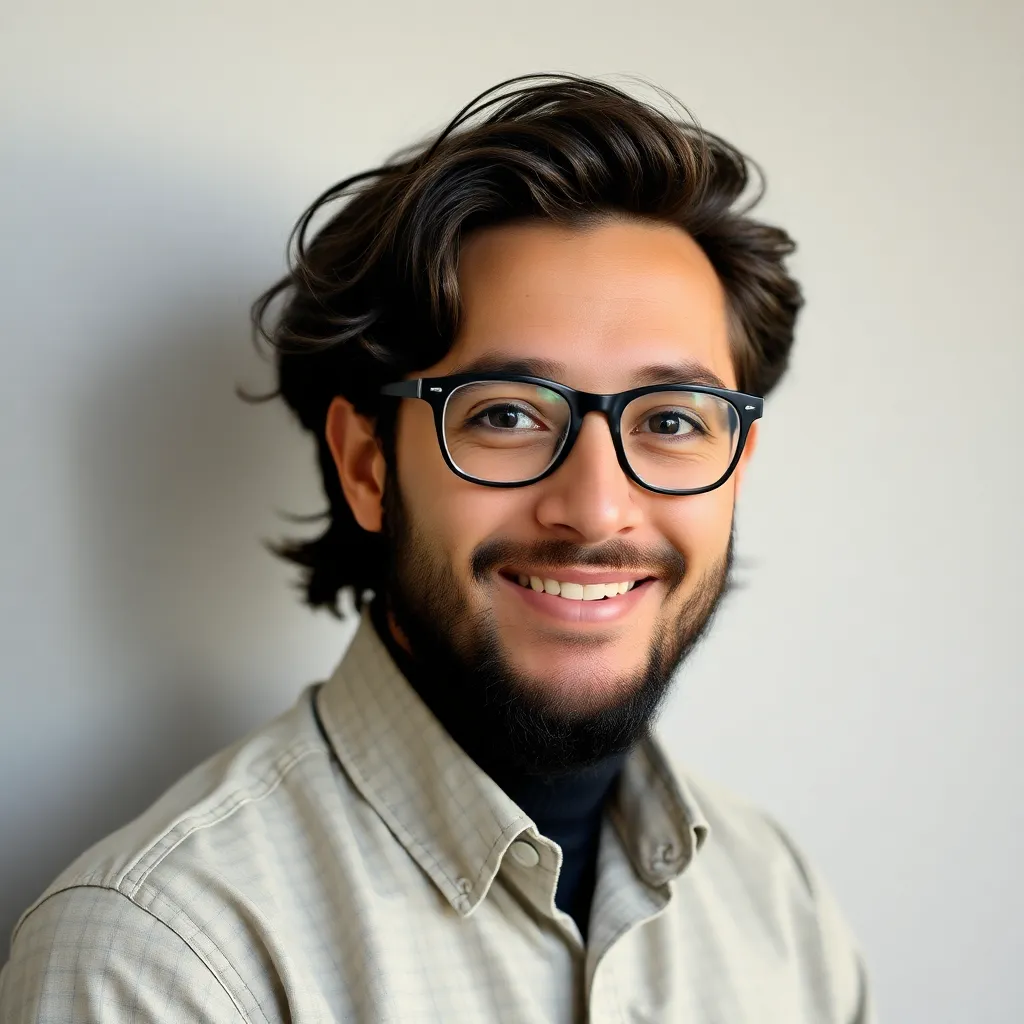
Onlines
May 08, 2025 · 7 min read
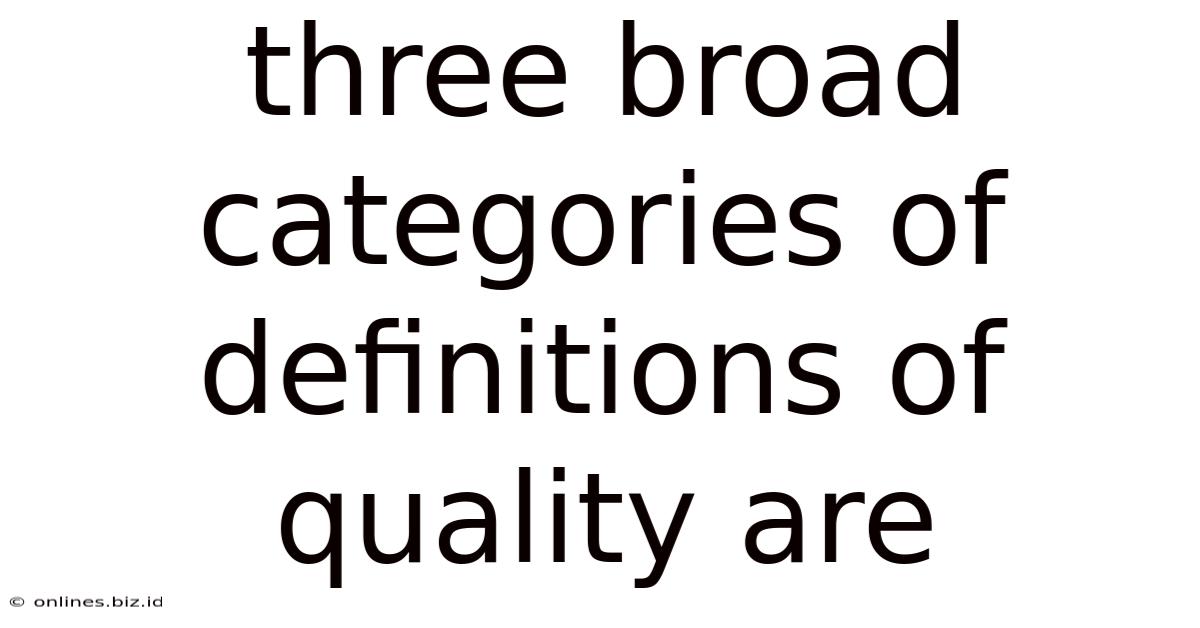
Table of Contents
Three Broad Categories of Definitions of Quality
Defining "quality" is surprisingly complex. While we all intuitively understand what constitutes high or low quality in various contexts, pinning down a universally accepted definition proves elusive. The concept shifts depending on the perspective – the producer, the consumer, or the overall societal impact. This article explores three broad categories of quality definitions: user-based, manufacturing-based, and value-based. We'll delve into each, highlighting their strengths, weaknesses, and practical applications.
I. User-Based Definitions of Quality
User-based definitions center on the customer's perception and experience. Quality is determined by how well a product or service meets or exceeds customer expectations. This approach emphasizes customer satisfaction and fitness for use. It's a subjective measure, varying significantly between individuals and groups.
A. Meeting Expectations: The Core Principle
The core of a user-based definition is the alignment between the product/service and the customer's expectations. These expectations can be explicit, such as those outlined in product descriptions or marketing materials, or implicit, stemming from past experiences, industry norms, and overall brand reputation. A product exceeding expectations leads to delight, while falling short results in dissatisfaction.
Example: A customer purchasing a new smartphone expects certain functionalities like camera quality, battery life, and processing speed. If the phone meets or surpasses these expectations, the customer perceives high quality. Conversely, if the camera is blurry, the battery drains quickly, and the phone lags, the quality is perceived as low.
B. Dimensions of User-Based Quality
Several dimensions contribute to the overall user perception of quality. These include:
- Performance: How well the product performs its intended function. This is arguably the most crucial dimension.
- Features: The specific attributes and functionalities offered by the product. More features don't automatically mean higher quality; they must be relevant and useful.
- Reliability: The consistency of performance over time. A product consistently delivering its promised function is seen as high quality.
- Conformance: How well the product meets its specifications and standards. This aligns with manufacturing-based definitions but retains importance from the user's perspective.
- Durability: The length of time the product remains functional before requiring repair or replacement.
- Serviceability: The ease and cost-effectiveness of maintenance and repair.
- Aesthetics: The visual appeal and overall design of the product. While subjective, aesthetics significantly influence user perception.
- Perceived Quality: This intangible dimension reflects the customer's overall impression and feeling about the product, often shaped by brand reputation, marketing, and word-of-mouth.
C. Measuring User-Based Quality
Measuring user-based quality involves gathering data directly from customers. Methods include:
- Surveys: Questionnaires assessing customer satisfaction with various aspects of the product/service.
- Focus groups: Group discussions providing in-depth insights into customer perceptions.
- Customer feedback forms: Simple forms allowing customers to express their opinions.
- Online reviews and ratings: Analyzing customer reviews on platforms like Amazon, Yelp, and Google.
- Social media monitoring: Tracking mentions of the product/service on social media to understand customer sentiment.
D. Strengths and Weaknesses of User-Based Definitions
Strengths:
- Customer-centric: Directly reflects the customer's experience, making it highly relevant.
- Actionable insights: Provides valuable feedback for product improvement and innovation.
- Competitive advantage: Understanding customer needs helps develop superior products and services.
Weaknesses:
- Subjectivity: Quality perceptions vary significantly, making it difficult to establish universal standards.
- Difficulty in measurement: Accurately capturing and quantifying customer perceptions can be challenging.
- Costly data collection: Gathering reliable customer feedback requires investment in resources and time.
II. Manufacturing-Based Definitions of Quality
Manufacturing-based definitions focus on the production process and the product's conformance to specifications. Quality is viewed as the degree to which a product or service meets pre-defined standards and tolerances. This approach emphasizes consistency, efficiency, and defect reduction. It's an objective measure, readily quantifiable through various metrics.
A. Conformance to Standards: The Guiding Principle
The cornerstone of a manufacturing-based definition is adherence to established standards. These standards can be internal (company-specific) or external (industry-wide or government-regulated). Quality control procedures aim to ensure that all products conform to these standards throughout the production process.
B. Dimensions of Manufacturing-Based Quality
Several key dimensions define quality from a manufacturing perspective:
- Product Specifications: The precise dimensions, materials, and other characteristics the product must possess.
- Process Control: The effectiveness of the production process in consistently creating products meeting specifications.
- Defect Rate: The percentage of defective products produced. A low defect rate signifies high quality.
- Yield: The percentage of successfully produced units compared to the total number of attempted units.
- Waste Reduction: Minimizing material and energy waste during production.
- Process Capability: The ability of the production process to meet specified tolerances consistently.
- Efficiency: Optimizing the production process to minimize costs and maximize output.
C. Measuring Manufacturing-Based Quality
Measuring manufacturing-based quality relies on objective data collected throughout the production process:
- Statistical Process Control (SPC): Using statistical methods to monitor and control the production process.
- Inspection: Examining finished products to identify defects.
- Testing: Subjected products to various tests to ensure they meet performance requirements.
- Quality Audits: Regular assessments of the production process to identify areas for improvement.
D. Strengths and Weaknesses of Manufacturing-Based Definitions
Strengths:
- Objectivity: Quality is measured through quantifiable metrics, leading to clear standards.
- Consistency: Ensures uniformity in product quality across production runs.
- Cost-effectiveness: Reducing defects and waste enhances profitability.
Weaknesses:
- Limited customer focus: May overlook customer needs and preferences.
- Narrow perspective: Focuses solely on the production process, ignoring other aspects like design and marketing.
- Rigid adherence to standards: May stifle innovation and hinder the creation of superior products that exceed expectations.
III. Value-Based Definitions of Quality
Value-based definitions integrate elements of both user-based and manufacturing-based approaches. Quality is perceived as the relationship between the product's benefits and its costs. This approach considers the customer's overall experience, the producer's efficiency, and the product's overall impact.
A. Balancing Benefits and Costs: The Central Idea
The core principle of a value-based definition is the optimal balance between the value delivered by the product/service and the cost incurred in acquiring it. This value includes not only functional benefits but also aesthetic appeal, convenience, brand reputation, and long-term ownership costs.
B. Dimensions of Value-Based Quality
Value-based definitions encompass several interconnected dimensions:
- Customer Value: The perceived benefits minus the perceived costs from the customer's perspective.
- Producer Value: The difference between the revenue generated from the product and the cost of producing it.
- Total Cost of Ownership (TCO): The total cost of acquiring, using, and disposing of a product, encompassing factors such as initial purchase price, maintenance, repair, and disposal fees.
- Life Cycle Assessment (LCA): Evaluating the environmental impact of the product throughout its entire life cycle, from raw material extraction to disposal. This addresses the societal impact of quality.
- Sustainability: Considering the long-term impact of the product on the environment and society.
C. Measuring Value-Based Quality
Measuring value-based quality involves a more holistic approach, integrating various quantitative and qualitative data:
- Customer surveys: Assessing customer perception of value.
- Cost accounting: Tracking the costs associated with producing and delivering the product.
- Lifecycle cost analysis: Estimating the total cost of ownership.
- Environmental impact assessments: Evaluating the product's environmental footprint.
- Market research: Understanding customer needs, preferences, and willingness to pay.
D. Strengths and Weaknesses of Value-Based Definitions
Strengths:
- Holistic approach: Considers both customer and producer perspectives.
- Long-term focus: Encourages sustainable practices and long-term value creation.
- Competitive differentiation: Allows companies to create unique value propositions.
Weaknesses:
- Complexity: More challenging to measure and quantify than other approaches.
- Subjectivity: The perception of value can still be subjective.
- Data availability: Gathering comprehensive data across multiple dimensions may be difficult.
Conclusion
The three categories of quality definitions – user-based, manufacturing-based, and value-based – offer distinct yet complementary perspectives on this multifaceted concept. No single definition encompasses every aspect of quality, and the most appropriate approach often depends on the specific context and priorities. A truly comprehensive understanding requires a balanced consideration of all three, integrating customer satisfaction, efficient production, and long-term value creation. By adopting a holistic approach, organizations can effectively manage quality, enhance customer satisfaction, improve profitability, and contribute to a more sustainable future. Understanding these varying definitions is crucial for companies seeking to build a strong brand, deliver high-quality products or services, and thrive in a competitive market.
Latest Posts
Latest Posts
-
Eng 130 Module Two Written Response
May 08, 2025
-
Which Medication Is Responsible For Neonatal Hypoglycemia
May 08, 2025
-
Cohesive Networks 2 Inc Andy Frain Services
May 08, 2025
-
A Type Ambulance Features A Conventional Truck Cab Chassis
May 08, 2025
-
Activity 1 1 5 Gears Pulley Drives And Sprockets Practice Problems
May 08, 2025
Related Post
Thank you for visiting our website which covers about Three Broad Categories Of Definitions Of Quality Are . We hope the information provided has been useful to you. Feel free to contact us if you have any questions or need further assistance. See you next time and don't miss to bookmark.