What Pneumatic Component Provides Straight Line Motion
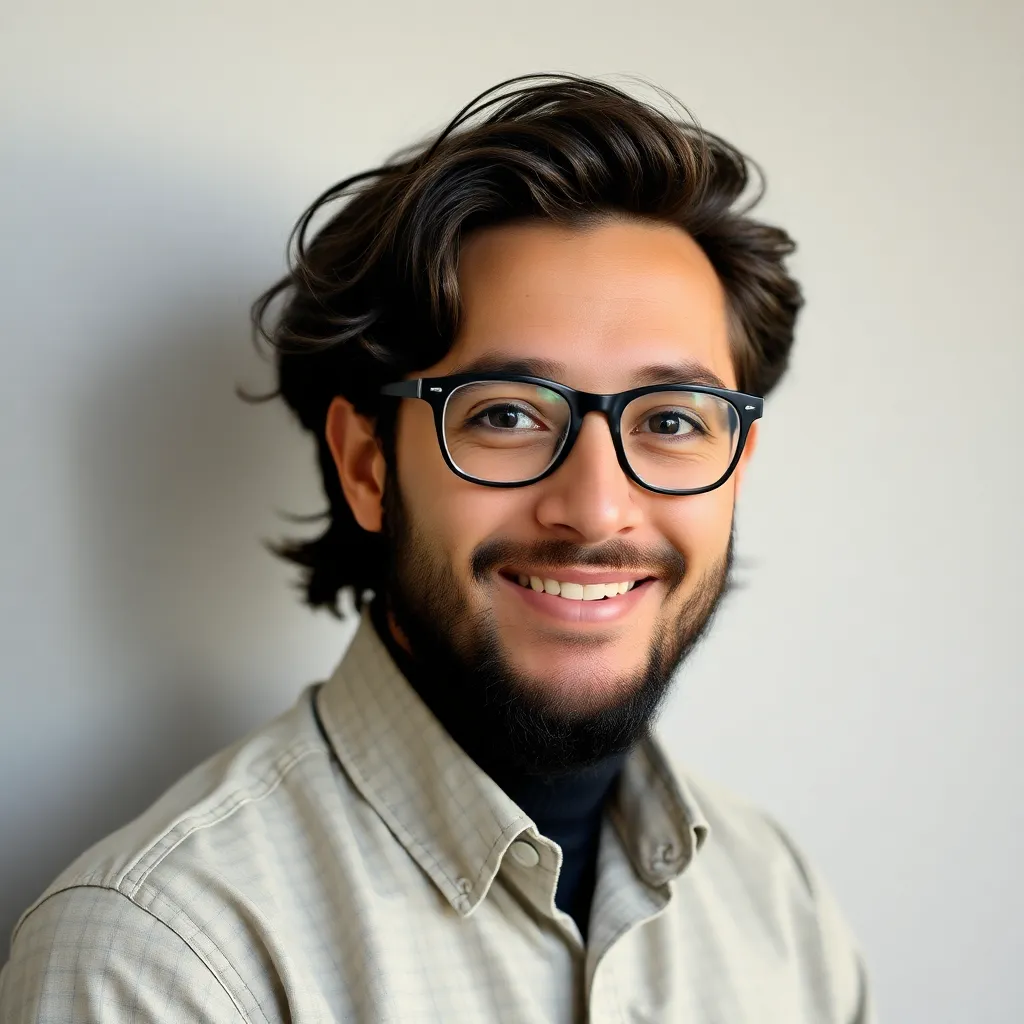
Onlines
May 09, 2025 · 6 min read
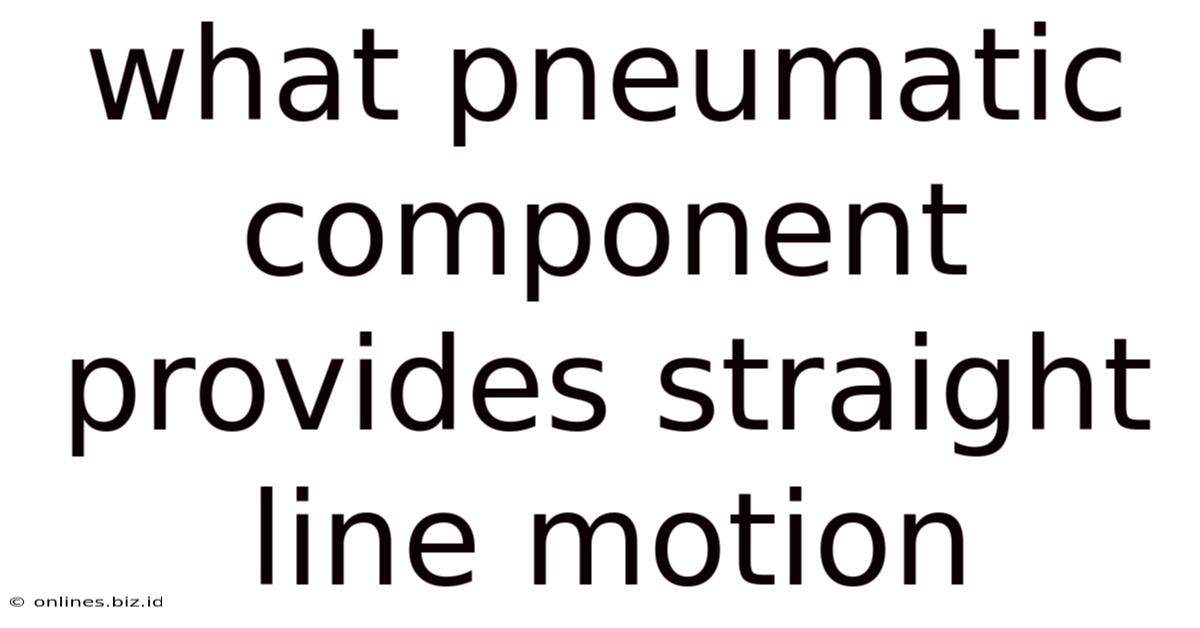
Table of Contents
What Pneumatic Component Provides Straight Line Motion? A Deep Dive into Pneumatic Cylinders
Pneumatics, the technology of using compressed air to power mechanical devices, offers a robust and versatile solution for a wide range of industrial applications. One of the most fundamental requirements in many pneumatic systems is the need for linear motion – moving a component in a straight line. The workhorse pneumatic component that fulfills this requirement is the pneumatic cylinder, often simply called an air cylinder. This article delves deep into the world of pneumatic cylinders, exploring their various types, applications, advantages, disadvantages, and selection criteria. We'll also touch upon related components and troubleshooting common issues.
Understanding Pneumatic Cylinders: The Basics
A pneumatic cylinder is essentially a mechanical device that converts compressed air energy into linear motion. It comprises several key components:
1. Cylinder Body (Barrel):
This is the outer casing, typically made of durable materials like aluminum or steel, which houses the piston and provides structural integrity. The barrel is precisely machined to ensure a tight seal with the piston.
2. Piston:
The piston is a cylindrical component fitted within the barrel. It's responsible for translating the compressed air pressure into linear force. Piston seals ensure a leak-free operation.
3. Piston Rod:
Extending from one end of the piston, the piston rod transmits the linear motion to the connected load or mechanism. It is usually made of hardened steel for durability and resistance to wear.
4. Air Ports:
These are the inlets and outlets for compressed air, usually located at the ends of the cylinder. They allow for controlled air flow to actuate the piston.
5. Seals:
Various seals (O-rings, U-cups, etc.) are crucial for preventing air leakage and ensuring efficient operation. Seal selection is critical based on the application’s pressure, temperature, and fluid compatibility.
Types of Pneumatic Cylinders: A Comprehensive Overview
Pneumatic cylinders come in a wide variety of designs, each suited to specific application requirements. The most common types include:
1. Single-Acting Cylinders:
These cylinders extend only under air pressure and retract through the force of a spring or gravity. They are simple, compact, and inexpensive, ideal for applications requiring only one directional movement.
- Advantages: Simple design, low cost, easy maintenance.
- Disadvantages: Limited force on the retraction stroke, relies on external force for retraction.
2. Double-Acting Cylinders:
These cylinders extend and retract under air pressure. Compressed air is supplied to either end of the cylinder to control the piston’s movement in both directions. They offer more versatility and control.
- Advantages: Bi-directional movement, greater control over speed and force.
- Disadvantages: More complex than single-acting cylinders, higher cost.
3. Tandem Cylinders:
These cylinders consist of two cylinders mounted together, allowing for increased stroke length or force. They are often used when a single cylinder cannot provide the required force or length.
- Advantages: Increased stroke length or force.
- Disadvantages: Larger size and higher cost compared to single cylinders.
4. Tie-Rod Cylinders:
These cylinders feature a robust construction using tie rods to connect the cylinder head and cap. This design offers high strength and rigidity, making them suitable for heavy-duty applications.
- Advantages: High strength and rigidity, suitable for heavy loads.
- Disadvantages: More complex assembly and disassembly.
5. Compact Cylinders:
These cylinders offer a smaller, more compact design, ideal for space-constrained applications. They are often used in robotics and automation systems.
- Advantages: Small size, space-saving design.
- Disadvantages: Limited force and stroke length.
6. Cushioned Cylinders:
These cylinders incorporate cushioning mechanisms at either end of the cylinder to reduce impact forces and extend the lifespan of the components. This is particularly important for high-speed applications.
- Advantages: Reduced noise and wear, improved lifespan.
- Disadvantages: Slightly more complex design, potentially increased cost.
Mounting Options and Accessories for Pneumatic Cylinders
Choosing the correct mounting style is crucial for optimal performance and safety. Common mounting options include:
- Trunnion Mounting: Offers a high degree of rigidity and is suitable for heavy loads.
- Flange Mounting: Allows for easy attachment to machinery.
- Clevis Mounting: Provides flexibility and is suitable for applications requiring angular movement.
- Foot Mounting: Suitable for simpler applications where stability is paramount.
Several accessories enhance the functionality of pneumatic cylinders:
- Magnetic Sensors: Provide feedback on piston position.
- Proximity Sensors: Similar to magnetic sensors, but suitable for non-magnetic pistons.
- Speed Controls: Regulate the speed of piston extension and retraction.
- Mufflers: Reduce noise generated during cylinder operation.
Advantages and Disadvantages of Pneumatic Cylinders
Pneumatic cylinders offer numerous advantages:
- Simple and robust design: Relatively easy to understand, maintain, and repair.
- High power-to-weight ratio: They can generate substantial force with a relatively light weight.
- Clean operation: Use of compressed air eliminates the risk of oil leaks and contamination.
- Fast response times: They can achieve rapid actuation speeds.
- Cost-effective: Generally inexpensive compared to other linear actuators.
- Easy control: Speed and position can be controlled using various pneumatic valves and accessories.
However, there are also some disadvantages:
- Compressed air requirements: Requires a compressed air supply, increasing initial investment and ongoing operating costs.
- Environmental impact: Compressed air generation and use can contribute to energy consumption.
- Sensitivity to temperature and humidity: Air pressure and cylinder performance can be affected by extreme environmental conditions.
- Noise: Pneumatic cylinders can generate significant noise during operation, although mufflers can mitigate this.
- Limited precision: Precision control of positioning can be challenging in some applications.
Selecting the Right Pneumatic Cylinder: Key Considerations
Selecting the appropriate pneumatic cylinder requires careful consideration of several factors:
- Bore Size: Determines the force the cylinder can generate.
- Stroke Length: The distance the piston travels.
- Mounting Style: Determines how the cylinder is attached to the machine.
- Operating Pressure: The pressure of the compressed air used.
- Operating Temperature: The ambient temperature range in which the cylinder will operate.
- Load Requirements: The weight and force of the object being moved.
- Speed Requirements: The desired speed of operation.
- Environmental Conditions: Dust, moisture, and other environmental factors can affect cylinder performance and lifespan.
Troubleshooting Common Pneumatic Cylinder Problems
Several issues can arise during pneumatic cylinder operation. Common problems and their potential solutions include:
- Leaks: Check seals, connections, and air ports for leaks. Replace damaged seals if necessary.
- Slow operation: Check for restrictions in the air supply, clogged air filters, or worn seals.
- Lack of power: Verify sufficient air pressure, check for leaks, or consider using a larger bore cylinder.
- Noise: Install mufflers to reduce noise or check for loose parts.
- Inconsistent operation: Inspect for damaged seals, incorrect air pressure, or problems with the control system.
Conclusion: Pneumatic Cylinders – The Powerhouse of Linear Motion
Pneumatic cylinders represent a fundamental component in the world of pneumatic automation. Their versatility, ease of use, and ability to provide reliable straight-line motion make them a preferred choice across a vast range of industrial settings, from manufacturing and packaging to material handling and robotics. By understanding the various types, their operational principles, and selection criteria, engineers and technicians can effectively leverage the power of pneumatic cylinders to build efficient and productive systems. Always remember to prioritize safety when working with compressed air systems and ensure regular maintenance to prolong the lifespan of your pneumatic cylinders. Proper selection and maintenance are key to maximizing the efficiency and longevity of these indispensable components.
Latest Posts
Latest Posts
-
For Inventoriable Costs To Become Expenses Under The Matching Principle
May 10, 2025
-
Partition Between Users Computer And Network
May 10, 2025
-
Nisa Life Of A Kung Woman
May 10, 2025
-
Timothy Works In The Graphic Arts Department
May 10, 2025
-
What Are The Two Processes Underlying This Image
May 10, 2025
Related Post
Thank you for visiting our website which covers about What Pneumatic Component Provides Straight Line Motion . We hope the information provided has been useful to you. Feel free to contact us if you have any questions or need further assistance. See you next time and don't miss to bookmark.