When Demobilizing The Pod If Equipment Is Missing You Should
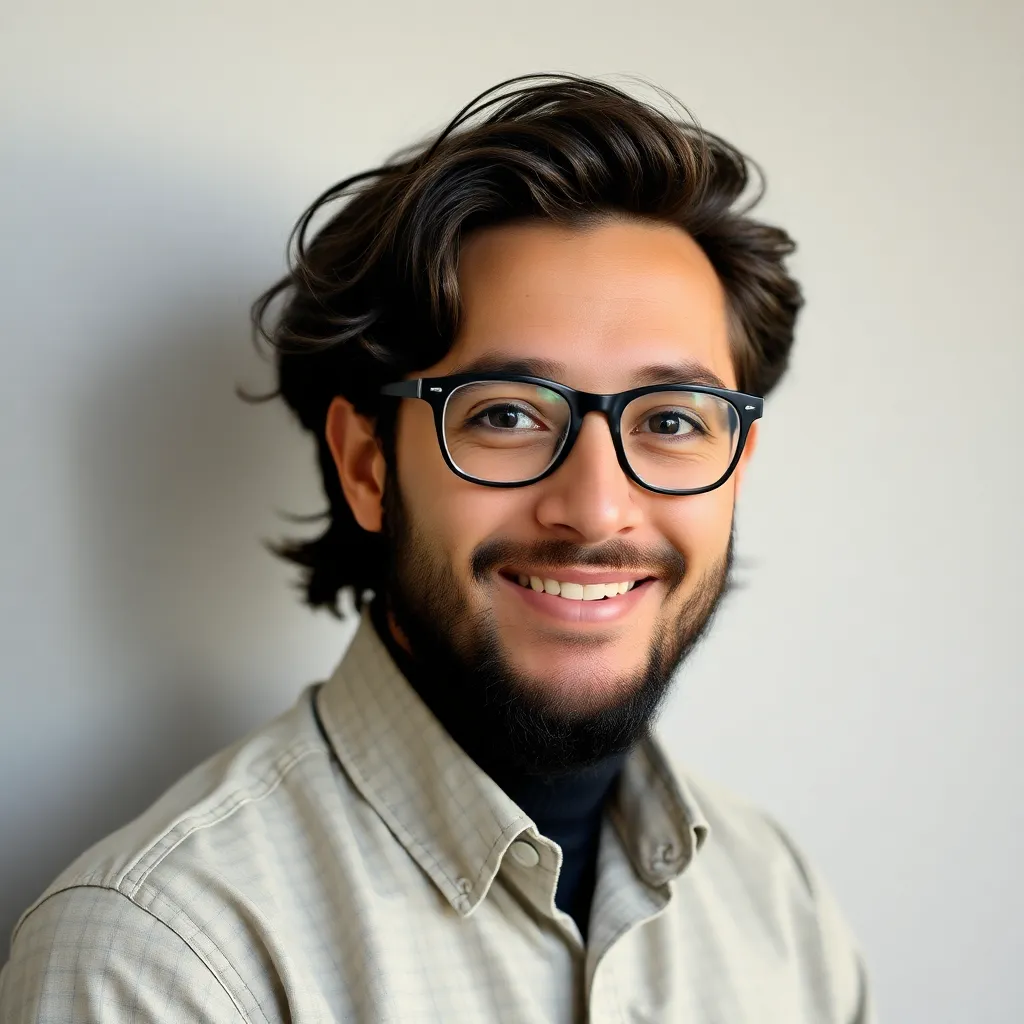
Onlines
Mar 10, 2025 · 6 min read
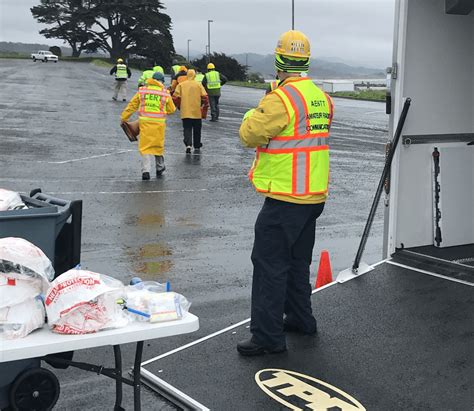
Table of Contents
When Demobilizing the Pod: Addressing Missing Equipment
Demobilizing a pod, whether it's a temporary worksite, a military unit, or a research expedition, requires meticulous planning and execution. A critical aspect of this process is accounting for all equipment. Missing equipment can lead to significant delays, financial penalties, safety hazards, and operational inefficiencies. This comprehensive guide explores the crucial steps to take when missing equipment is discovered during the demobilization process.
Understanding the Gravity of Missing Equipment
The consequences of failing to account for all equipment during demobilization are far-reaching. Let's explore some key implications:
Financial Ramifications:
- Replacement Costs: The most immediate consequence is the cost of replacing missing items. This can be substantial, depending on the nature and quantity of the missing equipment.
- Insurance Claims: Many organizations carry insurance to cover equipment loss or damage. However, filing claims requires thorough documentation, including a detailed inventory of missing items and circumstances surrounding their disappearance. Failure to provide this documentation can jeopardize a successful claim.
- Auditing Issues: Missing equipment raises red flags during audits. Auditors may question procedures, potentially leading to further investigation and penalties.
Operational Disruptions:
- Project Delays: Missing equipment can halt or significantly delay future projects that rely on those specific items. This can lead to missed deadlines, impacting productivity and profitability.
- Safety Concerns: Certain missing equipment might pose safety hazards. For instance, a missing safety harness can endanger workers, while missing communication devices can hinder emergency response.
- Reputational Damage: Failure to manage equipment effectively can damage an organization's reputation, affecting future contracts and partnerships.
Legal and Regulatory Implications:
- Non-Compliance: Missing equipment can indicate non-compliance with safety regulations or contractual obligations. This can result in fines, legal action, or suspension of operations.
- Liability Issues: If missing equipment contributes to an accident or injury, the organization may face legal liability.
Proactive Steps Before Demobilization Begins
Preventing missing equipment begins before demobilization starts. A thorough and well-organized approach is essential:
Comprehensive Inventory Management:
- Detailed Inventory List: Maintain a detailed, continuously updated inventory list throughout the pod's operational period. This list should include equipment ID numbers, descriptions, condition, location, and assigned personnel.
- Regular Inspections: Conduct regular equipment inspections to identify damage or missing items early. This allows for timely repairs or replacements, preventing escalation.
- Barcoding or RFID Tagging: Consider using barcoding or RFID tagging for accurate tracking and real-time inventory management. This technology minimizes human error and streamlines the inventory process.
- Digital Inventory System: Leverage digital inventory management software to centralize inventory data and enhance accessibility for all relevant personnel.
Clear Equipment Assignment and Responsibility:
- Designated Personnel: Assign specific personnel responsibility for each piece of equipment. This fosters accountability and simplifies the tracking process.
- Sign-Out Sheets: Implement sign-out sheets for equipment borrowed or used temporarily. This creates a clear audit trail for all equipment transactions.
- Regular Check-Ins: Establish regular check-in procedures to confirm equipment location and condition.
Secure Storage and Handling:
- Designated Storage Areas: Designate secure storage areas for equipment, minimizing the risk of loss, damage, or theft.
- Proper Packaging and Labeling: Ensure proper packaging and labeling of equipment for safe transport and storage.
- Maintenance Logs: Keep detailed maintenance logs for all equipment, including repair history and scheduled maintenance.
Responding to Missing Equipment During Demobilization
Even with proactive measures, missing equipment can still occur. Here's how to handle the situation effectively:
Immediate Actions:
- Stop and Investigate: When missing equipment is discovered, immediately halt the demobilization process. Conduct a thorough search of the pod's area to locate the missing items.
- Document Everything: Meticulously document all findings, including the date, time, location of the missing equipment, descriptions of missing items, and the names of personnel involved in the search. Take photographs or videos as evidence.
- Interview Personnel: Interview personnel who may have handled the missing equipment to gather information about its last known location and potential reasons for its disappearance.
- Review Inventory Records: Carefully review inventory records to trace the equipment's movements and identify any discrepancies.
- Expand the Search Area: If the equipment isn't located within the immediate pod area, expand the search to include surrounding areas.
Escalation and Reporting:
- Notify Supervisors: Report the missing equipment to your immediate supervisor and any other relevant authorities or stakeholders.
- Formal Incident Report: File a formal incident report outlining the situation, actions taken, and next steps.
- Internal Investigation: Initiate an internal investigation to determine the cause of the missing equipment and prevent future occurrences.
Recovering Missing Equipment:
- Retrace Steps: Attempt to retrace the steps of the equipment's movements to identify possible locations.
- Utilize Technology: Utilize tracking devices, GPS coordinates, or other technologies if applicable to locate missing equipment.
- Contact Local Authorities: In cases of suspected theft, contact local authorities to report the incident and initiate a formal investigation.
Lessons Learned and Preventative Measures:
After addressing the immediate situation, it's crucial to learn from the experience and implement preventative measures:
- Review Procedures: Conduct a thorough review of existing equipment management procedures to identify weaknesses and areas for improvement.
- Enhanced Training: Provide enhanced training for personnel on proper equipment handling, storage, and reporting procedures.
- Improved Technology: Invest in improved inventory management technology, such as RFID tracking systems or advanced software solutions.
- Accountability and Discipline: Enforce accountability for equipment handling and address any negligence or misconduct.
- Regular Audits: Conduct regular equipment audits to verify inventory accuracy and identify potential problems early.
Demobilization Checklist: Minimizing the Risk of Missing Equipment
To streamline the demobilization process and minimize the risk of missing equipment, create a detailed checklist covering the following aspects:
- Pre-Demobilization Inventory: Conduct a complete inventory count before commencing the demobilization process.
- Equipment Inspection: Thoroughly inspect all equipment for damage or missing parts.
- Equipment Cleaning and Maintenance: Clean and perform routine maintenance on all equipment before packing.
- Packaging and Labeling: Properly package and label all equipment for safe transport and storage.
- Transport and Logistics: Plan the transportation and logistics of equipment carefully, ensuring safe and secure movement.
- Designated Personnel: Assign specific personnel responsibility for supervising the demobilization of equipment.
- Final Inventory Check: Conduct a final inventory check after all equipment has been loaded and transported.
- Documentation and Reporting: Complete all necessary documentation and reporting requirements.
- Post-Demobilization Review: Conduct a post-demobilization review to identify areas for improvement.
By following these guidelines and implementing robust inventory management practices, organizations can significantly reduce the risk of missing equipment during demobilization, saving time, money, and preventing potential operational disruptions and safety hazards. The key is a proactive, well-planned, and thoroughly executed approach to equipment management throughout the entire lifecycle of the pod's operation.
Latest Posts
Latest Posts
-
Cold War Events And Policies Worksheet Answers
Mar 10, 2025
-
Ap Statistics Transformations To Achieve Linearity Worksheet
Mar 10, 2025
-
Match The Link State To The Interface And Protocol Status
Mar 10, 2025
-
Heming Way State Fall Camp Primitive
Mar 10, 2025
-
Which Pair Of Numbered Statements Best Completes
Mar 10, 2025
Related Post
Thank you for visiting our website which covers about When Demobilizing The Pod If Equipment Is Missing You Should . We hope the information provided has been useful to you. Feel free to contact us if you have any questions or need further assistance. See you next time and don't miss to bookmark.