With Regard To Suppliers Lean Systems Typically Involve
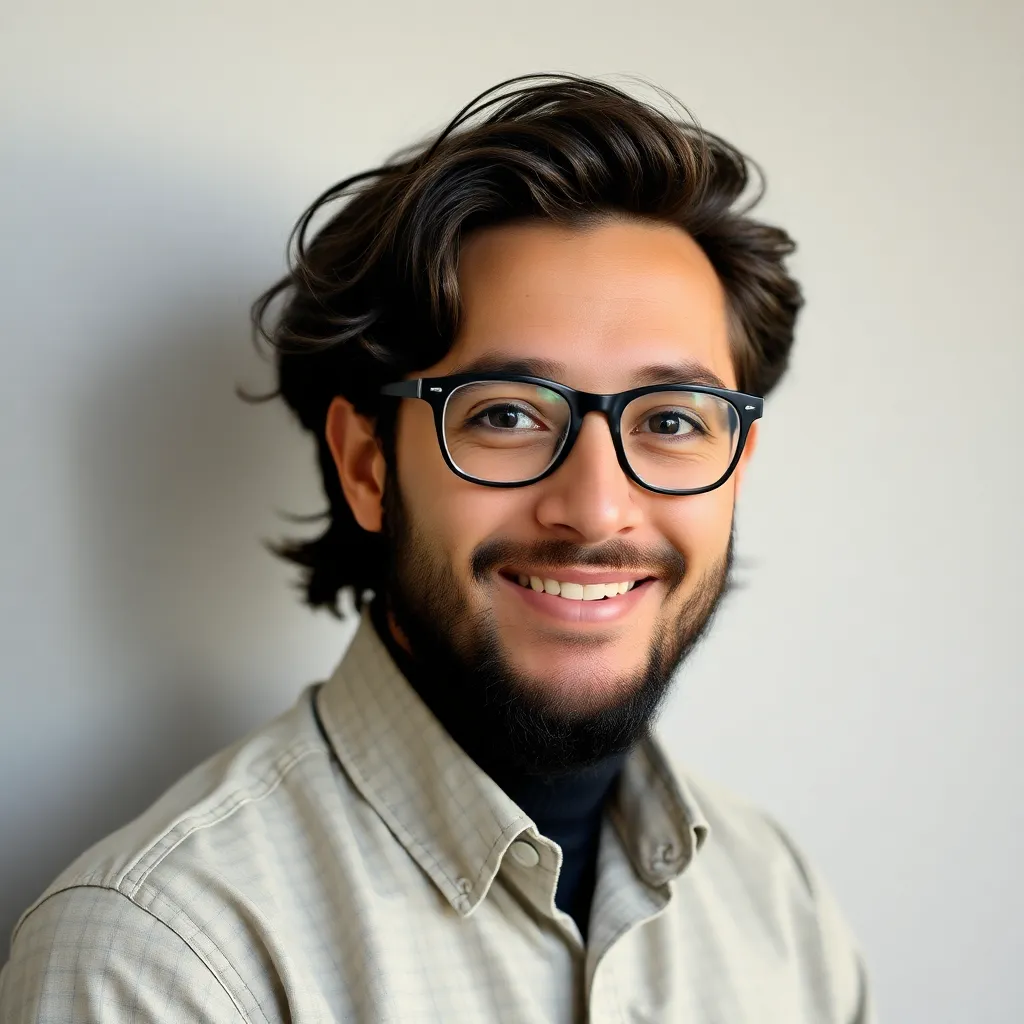
Onlines
May 09, 2025 · 6 min read
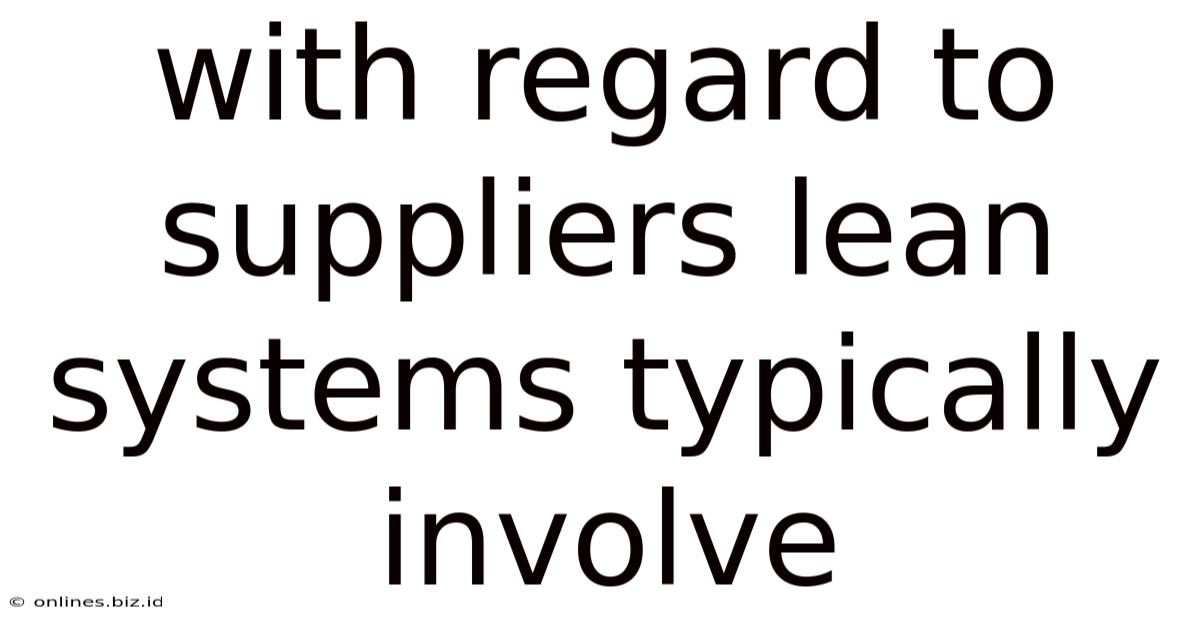
Table of Contents
With Regard to Suppliers: Lean Systems Typically Involve
Lean systems, focused on eliminating waste and maximizing value, significantly impact relationships with suppliers. Implementing lean principles necessitates a collaborative approach extending beyond internal operations to encompass the entire supply chain. This article delves into the crucial aspects of supplier involvement in lean systems, exploring the key strategies, challenges, and benefits of this collaborative approach.
Building Strong Supplier Partnerships: The Foundation of Lean
The core principle underlying lean supplier relationships is the establishment of strong, collaborative partnerships. This contrasts sharply with traditional adversarial relationships where suppliers are seen primarily as cost centers. Lean philosophy recognizes that suppliers are integral to the overall value stream and their performance directly impacts the final product's quality, delivery, and cost.
Key Strategies for Lean Supplier Integration:
-
Supplier Selection and Development: Lean principles dictate a meticulous selection process prioritizing suppliers demonstrating a commitment to lean principles themselves. This includes assessing their capabilities in areas such as quality control, just-in-time (JIT) delivery, and continuous improvement. Furthermore, ongoing development programs assist suppliers in enhancing their lean practices, fostering mutual growth and improvement.
-
Information Sharing and Transparency: Open communication and transparency are paramount. Real-time information sharing regarding demand forecasts, inventory levels, and quality issues enables proactive problem-solving and prevents disruptions. This requires implementing robust information systems and fostering a culture of trust and openness between the buyer and supplier.
-
Collaborative Problem Solving: Lean necessitates a joint approach to problem-solving. Instead of assigning blame, both buyer and supplier actively work together to identify root causes of defects, delays, or inefficiencies. This collaborative approach fosters innovation and enhances the overall efficiency of the supply chain.
-
Joint Improvement Activities (Kaizen): Participating in joint Kaizen events, focused on continuous improvement, is crucial. These events bring together teams from both organizations to analyze processes, identify waste, and implement solutions. This collaborative effort drives innovation and strengthens the buyer-supplier relationship.
-
Long-Term Contracts and Relationship Management: Lean systems often favor long-term contracts with key suppliers, fostering stability and encouraging investment in improvement initiatives. Dedicated relationship managers are assigned to cultivate strong, collaborative relationships, ensuring open communication and prompt resolution of issues.
Core Lean Principles in Supplier Management:
The implementation of lean principles within supplier relationships necessitates a deep understanding of core lean concepts. These concepts are not merely implemented individually but rather interwoven to create a holistic and synergistic approach.
1. Value Stream Mapping (VSM):
VSM is a powerful tool used to visualize the entire flow of materials and information from raw material sourcing to final product delivery. By mapping the entire value stream, including supplier processes, organizations can identify bottlenecks, waste, and areas for improvement across the entire supply chain. This collaborative approach allows for a shared understanding of challenges and opportunities, leading to more effective solutions.
2. Just-in-Time (JIT) Delivery:
JIT is a cornerstone of lean manufacturing, aiming to minimize inventory by receiving materials only when needed. This requires close collaboration with suppliers, ensuring precise delivery scheduling and exceptional quality control. JIT reduces storage costs, minimizes waste, and enhances responsiveness to market demands. However, it also necessitates a highly reliable and flexible supply chain.
3. Kanban:
Kanban systems use visual signals to manage the flow of materials and information. In supplier relationships, this could involve using Kanban cards to signal the need for replenishment, ensuring materials are delivered only when needed. This enhances visibility, improves communication, and prevents overstocking.
4. 5S Methodology:
The 5S methodology (Sort, Set in Order, Shine, Standardize, Sustain) focuses on workplace organization and efficiency. Lean principles extend 5S principles to supplier facilities through joint audits and improvement projects. This collaborative approach ensures a standardized level of organization and efficiency across the entire supply chain, leading to improved quality and reduced waste.
5. Poka-Yoke (Error-Proofing):
Poka-Yoke involves designing processes and systems to prevent errors from occurring. By working closely with suppliers to implement Poka-Yoke measures, organizations can drastically reduce defects and improve product quality. This requires a high degree of collaboration and a shared commitment to quality.
Challenges in Implementing Lean with Suppliers:
While the benefits of integrating lean principles with suppliers are significant, several challenges need to be addressed:
-
Resistance to Change: Suppliers may be resistant to adopting new processes and technologies. Overcoming this resistance requires patience, clear communication, and demonstrating the mutual benefits of lean implementation. Incentive programs and training can play a significant role.
-
Information Security and Confidentiality: Sharing sensitive data with suppliers requires establishing robust information security protocols and clear agreements on confidentiality. Trust and transparency are crucial for success.
-
Supplier Capabilities: Not all suppliers have the capacity or willingness to adopt lean principles. A thorough assessment of supplier capabilities is critical before embarking on a lean initiative. Supplier development programs can address capacity gaps.
-
Geographic Distance and Cultural Differences: Working with international suppliers can present challenges related to communication, cultural differences, and logistical complexities. Effective communication strategies and cultural sensitivity training are essential.
-
Measuring Performance: Establishing clear metrics for measuring supplier performance within the lean framework is crucial. These metrics must align with overall lean goals, and consistent monitoring and feedback are necessary.
Benefits of Lean Supplier Relationships:
The successful integration of lean principles with suppliers yields significant benefits across the entire supply chain:
-
Improved Quality: Lean principles lead to higher quality products and reduced defects due to enhanced process control and collaborative problem-solving.
-
Reduced Costs: Lean reduces waste, inventory holding costs, and transportation costs through JIT delivery and efficient processes.
-
Increased Efficiency: Streamlined processes and improved communication lead to greater efficiency throughout the supply chain.
-
Enhanced Responsiveness: Lean systems enable faster response to market demands and changes in customer requirements.
-
Stronger Supplier Relationships: Collaborative partnerships foster trust and mutual benefit, leading to stronger, long-term relationships.
-
Improved Delivery Performance: JIT delivery and efficient processes contribute to improved on-time delivery rates.
Conclusion: A Symbiotic Relationship
Integrating lean principles into supplier relationships is not a one-way street but a symbiotic partnership fostering mutual growth and improvement. While challenges exist, the benefits of a lean supply chain far outweigh the difficulties. By focusing on building strong, collaborative partnerships, implementing core lean principles, and addressing potential challenges proactively, organizations can realize the full potential of lean manufacturing and achieve a significant competitive advantage. The journey toward lean supplier integration requires commitment, patience, and a shared vision of continuous improvement, ultimately leading to a more efficient, responsive, and profitable supply chain. Continuous monitoring, evaluation, and adaptation are crucial for long-term success. The investment in building strong, lean supplier relationships pays off exponentially in the long run.
Latest Posts
Latest Posts
-
In Context Lines 6 7 I Loved Be
May 09, 2025
-
Statistics Is The Science Of Conducting Studies To
May 09, 2025
-
The Pancreas Of An Adult Client Is Located
May 09, 2025
-
Economic Catastrophes Occurred In All Of The Following Years Except
May 09, 2025
-
Which Of The Following Does Not Eat Other Biotic Factors
May 09, 2025
Related Post
Thank you for visiting our website which covers about With Regard To Suppliers Lean Systems Typically Involve . We hope the information provided has been useful to you. Feel free to contact us if you have any questions or need further assistance. See you next time and don't miss to bookmark.